Aptean Insights
Whether you’re looking for industry insights, product details, upcoming events or our latest news it’s all right here. Browse the categories below or get in touch with one of our experts if you have a question.
Results
Showing1-15of1976
- Blog Post Jul 3, 2025ERP for Discrete Manufacturing: Key Features That Drive Success in Every TeamGeneric ERP won’t cut it. Learn how AI-enabled discrete manufacturing ERP delivers the tools your teams need to drive efficiency, control and growth.
Learn More
- Success Story Jul 3, 2025Aptean Case Study BloApCo Industrial Manufacturing ERP WorkWise EditionBloApCo improved operations and planning with Aptean’s WorkWise Edition ERP, built for industrial manufacturing and ready for the cloud.
Download
- On-Demand Jul 3, 2025Webinar: Transforming the Fresh Produce Supply Chain: Expert PerspectivesHear from produce industry experts sharing real-world strategies to boost efficiency, enhance food safety and stay competitive. Don’t miss this chance to get practical insights tailored to your produce operation—save your spot today!
Watch replay
- Product Tour Jun 25, 2025Enterprise Asset Management: See Exactly How It WorksSee how our EAM software reduces downtime and repair costs while boosting asset performance. Watch the demo to explore automated work orders, real-time inventory tracking, and more.
Start My Product Tour
- Blog Post Jun 24, 2025Load Planning Software 101: Efficiency, Accuracy and the Power of AIBasic or free tools don’t cut it. Here’s why you need AI-powered load planning software built to optimize space, reduce spend and streamline logistics.
Learn More
- eBook Jun 23, 2025The Algorithm: What It Means To Be an AI-First CompanyThe future of manufacturing is AI-first. Download The Algorithm eZine to see how AI is reshaping the industry—starting now.
Download
- Blog Post Jun 17, 2025Stronger Together: Benefits of Apparel ERP Software for Every TeamConsumers today shop online more than ever. Apparel ERP software can help you apparel business go-to-market online faster. Find out how, now.
Learn More
- On-Demand Jun 17, 2025Aptean Fresh Produce ERP in Action—An In-Depth Look at the Next Generation of Produce Pro SoftwareThe next generation of Produce Pro Software is here. In this demo, our experts show how growers, packers, and shippers can use modern, produce-specific tools to streamline tasks, enhance traceability, and boost efficiency.
Watch replay
- Blog Post Jun 12, 2025TMS Implementation Done Right: Your Step-By-Step Survival GuideDon’t let your TMS rollout stall out. This no-fluff guide gives you a clear, step-by-step plan to sidestep common pitfalls and drive real value.
Learn More
- Blog Post Jun 10, 2025How To Justify Manufacturing Technology Investment Amid Economic UncertaintyMaking the case for manufacturing software is tough—especially during economic uncertainty. Here's how to justify the spend with confidence.
Learn More
- Product Tour Jun 10, 2025Transportation Management System: Your Instant WalkthroughTake this interactive tour of our TMS software features—including carrier selection, truckload options and load planning.
Start My Product Tour
- Brochure Jun 6, 2025Made2Manage Edition ERP Software for Today’s Manufacturers: BrochureAptean Made2Manage ERP empowers discrete manufacturers to streamline operations, optimize supply chains, and make smarter decisions—now enhanced with AI-driven automation and insights via Aptean AppCentral.
Download
- Success Story Jun 5, 2025Aptean Apparel ERP and PLM Full Circle Edition, Case Study: Jantzen BrandsJantzen Brands enhances efficiency and collaboration by streamlining operations with Aptean's Apparel ERP and PLM solutions—driving smarter decisions from design to delivery.
Download
- Blog Post Jun 5, 2025How a Transport Management System Empowers Your Entire OrganizationA TMS isn’t just for logistics—find out how it automates processes and drives smarter decisions for every department, from purchasing to the C-suite.
Learn More
- Blog Post Jun 3, 20255 Steps to Create Excellent Food Product Traceability ProceduresWe all know how important food product traceability is, but how do you go about securing it? These five simple steps will help you establish clear procedures.
Learn More
Ready To Start Transforming Your Business?
We’ve got the specialized industry software to help your organization thrive.
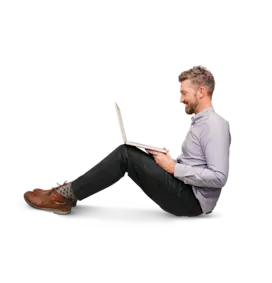