The Role of Enterprise Asset Management as a Digital Transformation Tool
The Role of Enterprise Asset Management as a Digital Transformation Tool
The Role of Enterprise Asset Management as a Digital Transformation Tool
20 Sep 2022
Kay Jenkins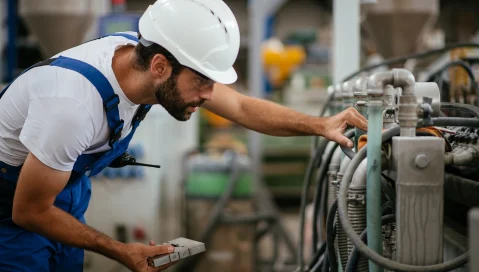
In today’s manufacturing industry, you must deal with rising material and wage costs, labor shortages, supply chain disruptions and increased customer expectations. In addition, you need to ensure that your operations are consistently performing at peak levels to remain competitive. After all, one downtime incident can cost your company up to $17,000 per year.
How can you compete without breaking the bank? The answer—enterprise asset management software (EAM). EAM will help you keep maintenance costs down while making the most of the resources you have. But, where your EAM will really accelerate your business is that it helps support even the most traditional manufacturing companies become more efficient, both by enhancing production output and optimizing assets throughout their lifespan.
Manufacturers are working toward the goal of digital transformation, which is using the right technology to help you maximize your revenue while reducing operational costs and improving production agility.
In the article below, we’ll explore briefly what an EAM does and examine how a modern EAM solution plays a crucial role as a digital transformation tool for manufacturing companies.
What Does EAM Do?
EAM is a complete asset lifecycle management solution that helps with managing your assets from procurement to scrap. A robust EAM system allows you to keep tabs on asset health and behavior and will help you get the most out of your investment. Critical equipment you need to sustain production, services and operations will benefit from using an EAM as you’ll get more out of production; maintenance costs will be lower; and your assets will simply last longer.
Moreover, with an EAM, you can analyze data and create reports to detect key trends and anomalies, find performance issues and make data-driven decisions. For example, the reporting and analytics tools in EAM will help you to decide if it makes more sense to repair the machine or buy a new one.
Below are a few key benefits you can expect right away by implementing an EAM:
Centralize asset information enabling better decision making.
An EAM system keeps all asset information, maintenance planning and history, and spare parts inventory information in one system. With consolidated asset records, maintenance managers can quickly see asset location, assess the condition, check maintenance schedules and see which technicians are available to resolve the issue. An EAM automates workflows so that they are accessible to everyone in the organization.
Resolve issues before they happen.
EAM software gives companies a preemptive approach to maintenance called preventive maintenance. Preventive maintenance strategy helps your assets run more efficiently and reduces asset downtime with plant operations remaining consistent and stable with fewer costly disruptions. With EAM, you can automate preventive maintenance scheduling by performing periodic, proactive inspections that help prevent machine failures from occurring.
With your EAM, you can set up maintenance schedules on your timetable, based on data from within your enterprise. Robust analytics and reporting in the EAM will give you the information you need to set up the most efficient and cost-effective maintenance schedule for your operation even if you have multiple plants.
Maximize asset utilization.
EAM will collect both historical and real-time data from analytical and diagnostic tools to help you extend the availability, reliability and usable life of physical assets. For many asset-intensive businesses, equipment that is decades old may still be operating and will require parts during routine maintenance. Therefore, an EAM is imperative as these older assets are still crucial to production and the cost to replace them could be formidable. By keeping all assets on a proactive maintenance schedule, EAM helps to ensure peak performance of all your equipment, no matter the age.
Asset-intensive business owners like you have invested considerably into your assets, and you need to ensure that you are getting the most for your money. Therefore, you need to schedule, monitor and control asset use. With EAM software, you can manage how and when assets are used, and analyze the financial impact; make the best use of your assets and save on unnecessary downtime for unneeded repairs.
What Makes EAM an Ideal Digital Transformation Tool?
Diligent manufacturers must control and plan asset maintenance while maintaining constant production across the entire enterprise. The old ways of managing assets and maintenance activities just won’t do—paper based, disparate methods are time consuming and counterproductive. EAM is an accelerant digital tool that augments the capabilities of a plant – capabilities like automation and advanced analytics to improve output and lower costs.
If you want to gain an edge in manufacturing—and managing your maintenance—now is the time to embrace your digital transformation and implement an intelligent solution to drive new levels of agility and efficiency. EAM provides the insights you need to make informed decisions regarding your equipment, creating greater efficiency and improving productivity within your operations.
Let's look below at two more advantages of including EAM within your digital transformation journey: plant profitability and operational visibility.
1. EAM Boosts Plant Profitability
Manufacturers get more efficient factories and smart manufacturing processes with preventive maintenance technologies. This allows them to improve output, quality and delivery while reducing operational costs. It’s as simple as this: well-maintained machines work better and break down less often, just like how a car that gets regular oil changes and repairs will perform better.
Machines that run consistently at peak performance improve production operations. With EAM, you’ll get a reduction in maintenance costs, because robust, timely maintenance programs prevent costly issues and downtime from arising which in turn boost profitability. And when an asset reaches the end of its lifecycle, you can expedite implementing a replacement. Improved maintenance operations lead to timely production and improved quality, all of which leads to more money to put back into the business and help you grow.
2. EAM Enhances Operational Visibility
As mentioned earlier, an EAM system gives you a complete overview of critical assets, their current condition, their warranty and service information, and other relevant details. Thereby:
You gain insight into the health of your assets.
You gain visibility into all active maintenance work orders.
You gain visibility into future orders and can plan and prioritize activities.
With EAM, your team will be able to spend time working on high-value tasks. You won’t have extra parts inventory and you won’t duplicate tasks.
EAM Is the Answer
Manufacturers using a siloed approach to maintenance processes with disparate technology systems will be left behind their competitors. Companies that want to remain competitive must have this full operational visibility into asset management processes. In some manufacturing enterprises, processes are still manual and paper intensive and every department keeps separate records in a jumble of databases or spreadsheets.
Sure, it’s possible to function that way—many manufacturers do. But this approach, without communication between teams, often causes duplicate efforts. Data entry is an inefficient, manual process. Planning processes are stunted. Business intelligence is nonexistent. And, without business intelligence, you cannot implement process improvements, nor make meaningful strategic business plans.
A robust EAM solution can help manufacturers overcome all these challenges. The truth is, EAM can accelerate digital transformation for manufacturers, and the tools you need to do it are readily available, affordable and easy to implement.
Manage and maintain critical assets with Aptean EAM using preventive maintenance strategies and advanced analytics to optimize performance, extend asset lifecycles and reduce operational downtime and costs. Want to learn more about how EAM can future-proof your business? Reach out—we’d love to talk.
Related Articles
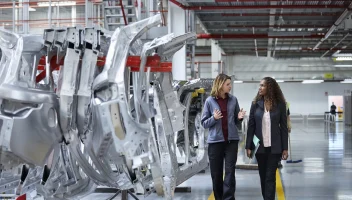
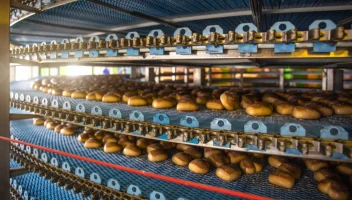
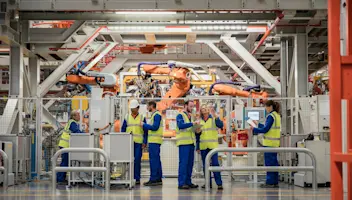
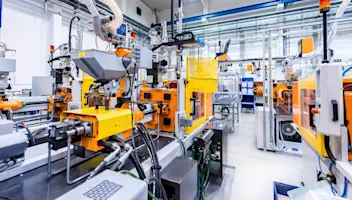

Your Ultimate Guide to Plant Optimization and Managing Costs
To remain competitive, enterprises need proven methods to get the most out of their current assets, avoid downtime and plan for contingencies.
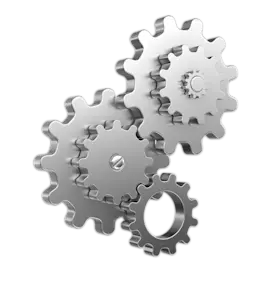