Stop, Collaborate and Listen: How Factory MES Transforms Your Shop Floor
Stop, Collaborate and Listen: How Factory MES Transforms Your Shop Floor
Stop, Collaborate and Listen: How Factory MES Transforms Your Shop Floor
3 Dez 2019
Aptean Staff Writer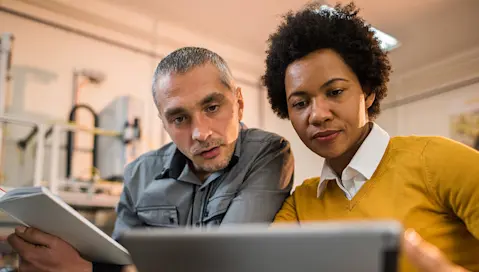
Factories often experience the same issues over and over again. With such a diversity of equipment to support and an ever-changing labor force to manage, knowing which corrective action to deploy and who to communicate with can be difficult for any employee to stay on top of.
Enter the infamous red book — the binder of recorded issues and notes passed from shift to shift with the intention of housing information on how to resolve these issues quickly if they happen again. While the irony is likely not lost here, more often than not organizations operate under these processes.
As an example, let’s say your Line 1 Filler nozzle number three has jammed for the second time this week. Every time it malfunctions, workers either have to relearn the problem because there are no records of the previous collaboration and actions, or they have to hunt for the solution because the records are spread across multiple channels. Or the necessary information is buried behind other notes and data within the red book.
This kind of reactionary problem solving doesn’t work in the long term; it only solves the problem temporarily. And when nozzle number three jams again, it’ll have to be fixed all over again. It’s a clunky and painstaking process.
In many plants, there are ten different ways workers might communicate about a single issue (messages, emails, projects, meetings, scribble notes, SMS/radio, tasks, C.I/Kaizen, huddles, word of mouth, and the list goes on and on). These are all effective methods of communication, but when they exist in disparate systems, they are all, in effect, different channels of workarounds. When communication is inconsistent and across multiple platforms, it’s really hard to be efficient. So how do you go about solving this problem?
The Three Cs: Collaboration, Consistency and Communication
Collaboration is key for any organization looking to improve operations, but in a production environment where seconds and minutes of lost productivity can directly affect your bottom line, streamlining these processes becomes just as critical as the act of collaboration. You need a system to help manage and track the data, address the problem head-on, and communicate all of this in a clear and concise way.
By leveraging a manufacturing execution system (MES) with a collaboration engine built into the platform, organizations are equipped with tools to consolidate these sources into one, easily accessible view. Individuals across the organization are able to work together with a common purpose. Now there’s more consistency in the process and communication becomes clearer as a result.
Why is this essential for the success of your business? For several reasons, really:
It gives teams a voice. There’s now room for conversation and discussion.
Users are messaging people as opposed to departments. This makes it easier to assign responsibility to a single person; there are fewer assumptions that someone else in the team is going to manage the problem.
There will be an increased speed of resolution.
There is now evidence on which users can track the progress and prognosis of an issue.
The production environment is now one that’s based on a performance culture. It’s an environment where everyone is expecting that level of collaboration. If that’s the culture, there’s no room for excuses because people already expect you to be dynamic.
Messages, Tasks and Notes
With a purpose-built MES solution, all of those various means of communication are boiled down into a single platform that includes three essential communication and collaboration features: messages, tasks and notes. These three things together can help to more easily solve whatever problem operators, supervisors and executives face in their factories. Let’s further explore their functionality on the Factory MES platform:
Messages - To continue with the example from above, if nozzle number three is broken, you need to message the supervisor in charge of the bottling lines in real-time to alert him/her of the problem. With the ability to send a message to a person rather than a department, the communication is far more valuable, and it eliminates room for miscommunications about who has assumed the responsibility for correcting the problem.
Tasks - On the tasks interface, the user assigns the task to a specific person so everyone knows who is now responsible for correcting the problem.
Notes - These are essentially digital sticky notes. You can stick a note against a machine, a product, an employee, a part, etc. The notes section functions the same way the red book does for factory workers between shifts. It’s where they log their notes in between each shift, add photos as evidence, and provide details of the issue – only this is digitized and all the information, so long as it has the threaded title (the same one from messages), is associated with the same issue.
Generally, when there’s a problem, it needs to be solved quickly. This is how businesses avoid production delays and excess costs. Aptean’s Factory MES solution fosters smart collaboration and real-time communication across all levels of the organization, which is critical for the success of food and beverage manufacturers. All of this collaboration data can also be easily used in your Continuous Improvement Campaigns to have a fuller picture around problems, root causes and solutions.
With a system that has built-in collaboration functionality, all reporting is documented. So, instead of repairing the same nozzle every three months, any recurrence of the same issue may be resolved faster or, better yet, avoided entirely. This is because communication is clear. Because consistency is simpler. Because collaboration is paramount.
We’re connecting the dots between data and information, and best of all, we’re putting all of the focus on you and your company through effective collaboration.
Ready to say goodbye to efficiency-draining workarounds and miscommunications? Get in touch with our team of MES experts today.
Sind Sie bereit, Ihr Unternehmen grundlegend zu verändern?
Wir bieten Ihnen die spezialisierten ERP-Lösungen, die Sie für die Herausforderungen Ihrer Branche benötigen.
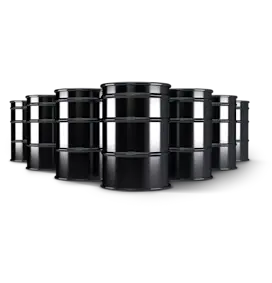