Stock Picking Made Easy with Print Shop Management Software
Stock Picking Made Easy with Print Shop Management Software
Stock Picking Made Easy with Print Shop Management Software
13 Nov 2020
Aptean Staff Writer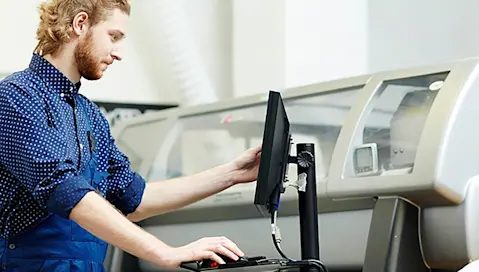
As a production or stock picker for an apparel decorating or a promotional products company, your job consists of picking individual items to fulfill customer orders. In this important role, you want to ensure that you have the tools available to complete your picking tasks accurately, quickly and efficiently to meet customer expectations. Print shop software with an integrated warehouse management system (WMS) provides the technology to direct stock picking with a variety of software functionalities to make your job easier.
Why is Warehouse Picking Important?
As an essential aspect of order fulfillment, picking is one of the most expensive and labor-intensive activities in the warehouse. Because of its direct impact on customer satisfaction, business reputation and profitability, maximizing picking efficiency is a priority for most print shops. Without a WMS, your job may regularly result in inaccurate picking due to simple errors, inconsistent labeling or moved inventory – causing increased production time and a loss of company profits.
How Stock Pickers Use WMS
To ensure efficient order fulfillment for your customers, printing company software with an integrated WMS utilizes barcodes and hand-held scanners that provide real-time updates and accurate visibility of warehouse inventory. The scheduling queue within the software provides each stock picker with their scheduled list of jobs for their shift on a priority or date basis, including which orders to fill for customers, and in what order to do so.
Readily displayed on the device are the order details (SKU, description, warehouse or bin location, quantity) helping you to find items quickly – presenting details in an optimal pick path within the warehouse to minimize unnecessary movement and backtracking. Scanning items and bin locations ensure accuracy, as the system alerts you if selecting the incorrect item. When all items for an order have been acquired, the sales order ticket is printed and the order is ready for the next stage of the production process.
Benefits of a WMS System for Stock Pickers
Reduces reliance on manual/paper methods – With a WMS, there is little wasted labor and fewer costs associated with utilizing paper processes. This lessening of manual methods lowers the opportunity for keying erroneous information and therefore decreases the chance of errors in customer orders. By removing the need for visually scanning of labels, the speed and accuracy for stock pickers of all skill levels are improved.
Enhances inventory accuracy – As your picking activities are streamlined by scanning barcodes for customer orders, automated tracking accurately deducts products from inventory counts in real-time. This provides optimal accountability and inventory accuracy as inventory updates occur immediately.
Optimizes picking – You will move more efficiently, improve your picking time, and pick orders more accurately through the warehouse with a WMS solution that optimizes the picking order so that you only visit each bin, rack and warehouse location once – reducing the amount of walking or retracing your steps. The system also updates picking orders with new locations when bins are moved to a more centralized location due to high demand or excess of inventory was ordered and overflow needs to be picked first.
Improves customer service – Printing business software integrated with WMS helps increase customer service and satisfaction levels, as stock pickers can deliver accurate customer orders on-time more often. Knowledge about inventory levels helps limit the amount of out-of-stock products and backorders, therefore minimizing customer frustration. Customer service reps have the advantage of transparency – knowing when order picking is occurring to provide real-time status information to customers to keep them informed.
Completing your daily stock picking tasks accurately and efficiently for your apparel decorating or promotional products’ company is essential for your business to remain competitive. Utilizing print shop management software integrated with a WMS system helps to make your regular stock picking tasks easier and increases visibility across the organization.
Our print shop management solution, Aptean Impress ERP, can provide stock pickers with the tools they need to streamline their tasks and keep customers happy – contact us for a demonstration today.
Ready to start transforming your print shop business?
We’ve got the specialised industry software to help your organisation thrive.
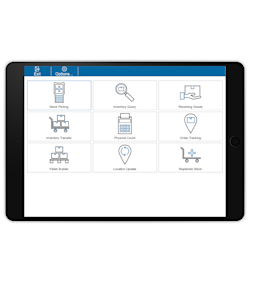