Aptean Smart Hub Case Study: Bongards Creameries
Aptean Smart Hub Case Study: Bongards Creameries
Aptean Smart Hub Case Study: Bongards Creameries
Mar 28, 2023
Titular
- Bongards Creameries Saves Time, Streamlines Processes and Drives Continual Improvement With Aptean Smart Hub
Bongards Creameries is a vertically-integrated global supplier of both natural and processed cheeses, as well as powdered whey, with hundreds of millions of pounds of finished goods manufactured at its two production facilities in Minnesota and a third in Tennessee.
Founded in a small, southern Minnesota town, the 300-farmer co-op has a diverse range of clients from food service distributors to commercial restaurants, retail delis, schools and convenience stores.
The Challenge
In the past, multiple departments at Bongards were burdened with time-intensive tasks. The lack of automation in many processes and connectivity across the company’s tech stack resulted in inefficiencies and prevented employees from focusing on more important matters. Some of the challenges included:
Manual processes consuming team members’ valuable time and leaving room for error
Lack of visibility across multiple solutions for different operational areas
Need for greater insight into potential issues before problems occur
The Solution
To solve these challenges, the Bongards leadership team chose to implement Aptean Smart Hub, a solution designed to automate processes, enable system integrations, promote data accessibility and increase collaboration across the entire organization. Bongards’ staff have leveraged it more and more to tie together various software and web services while also automating tedious manual processes.
Smart Hub enabled Bongards to set up more automated alerts for order status, new customer setup, past due invoices, electronic data interchange (EDI) issues and financial period rollovers—helping keep employees informed, engaged and ahead of urgent matters.
“Shipping and logistics have improved thanks to the automatic sharing of data. Aptean Smart Hub integrates Aptean Process Manufacturing ERP and our TMS and automates processes, so our employees don’t have to worry about entering manual orders.”
The Result
Bongards quickly unlocked considerable benefits thanks to the decision to deploy Aptean Smart Hub, but that was only the beginning. The solution has had a positive impact across a number of operational areas via automation, and the business continues to unlock additional operational advantages as staff leverage new features and functionalities. Those benefits include:
Time saved and mistakes prevented thanks to intelligent, automated processes
Cohesive solution ecosystem via integrations between platforms
Automatic alerts based on predefined criteria keep employees in-the-know
Automation of Accounting and Finance Procedures
With Aptean Smart Hub’s auto-invoicing process replacing time-intensive manual tasks, Bongards’ account receivable team saved approximately 23 hours of work in a three-month period while also helping to prevent mistakes in manual data entry.
In addition, other automated processes built with Smart Hub are taking care of uploading invoices to the Document Connect service so there’s a record of them in the ERP system, as well as emailing them and the associated bills of lading to customers.
“That would be basic clerk work for the people who are accounting specialists,” said Bob Grinsell, IT Business Analyst. “Smart Hub allows them to put their time to a much more valuable use. It alleviated the need for them to act as data handlers, letting them actively investigate and correct the root causes of issues.”
Proactive Visibility With Automatic Alerts
Beyond automations, Smart Hub also delivered significant benefits for Bongards with the deployment of automatic alerts. Business teams can stay ahead of potential complications—like a customer reaching their credit limit—and come to a solution that works for all parties involved.
Alerts have also been set up for data hosted in Document Connect, using pre-defined criteria to flag errors and resolve discrepancies in official records—helping to ensure the internal database is accurate and keeping orders, inventory and financials aligned.
“It looks at the data, analyzes it and alerts certain team members if conditions are met. We didn’t have that capability before Smart Hub—we didn’t have any system at all that would look at data and send out a notification to alert someone.”
Conclusion: Seamless Integration Across the Organization
Aptean’s solution specialists were able to help Bongards ensure seamless links between several systems including Aptean Process Manufacturing ERP and the company’s transportation management system (TMS). These integrations help keep all parts of the company on the same page and relieve individual workers of having to manually re-enter information when moving from one system to another.
Alongside the out-of-the-box benefits listed above, these integrations help increase operational efficiency and allow Bongards to focus on driving business growth. And, Smart Hub’s user-friendly, intuitive interface and knowledge repository ensure that the team can continue to iterate on existing automations and alerts, as well as deploy additional improvements to drive further success.
“You don’t have to continually reinvent the wheel. You can take an existing customization and modify it to do something else. You’re not starting from scratch on everything you want to achieve—there’s a whole library of things you can reference and use to implement something a lot more efficiently and a lot faster.”—Bob Grinsell, IT Business Analyst, Bongards Creameries
Ready To Be the Cream of the Crop With Aptean?
With exacting customers, complex inventory needs, and a raft of regulations and safety requirements to adhere to, food and beverage organizations need advanced solutions to power their digital transformation journeys. Generic solutions just won’t cut it. And one-size-fits-all providers are no good.
Enter Aptean. With decades of experience in the food and beverage industry under our belt, we’re able to provide industry-specific solutions that cater to your needs straight out of the box. From offering automations and improving efficiency to enhancing customer service and driving profitability, we’ve got a system to propel your business forward, including our tailored food ERP, advanced TMS tools and robust product lifecycle management (PLM) software.
And, even better, it’s all backed by our expert in-house teams, who “speak your language” and offer by-your-side support to help your business meet its operational goals. What’s more, many of our solutions are offered with cloud deployments on the Software as a Service (SaaS) model so that you can benefit from greater security, enhanced scalability and improved accessibility.
Ready to take the next step on your digital transformation journey with Aptean? Get in touch with our experience teams today or view our full range of food and beverage software.
You can also read more success stories from companies like Bongards Creameries to see how your company could benefit and start seeing speedy return on investment (ROI).
¿Listo para soluciones específicas para el sector que impulsan resultados?
Nuestro sistema de ERP especializado en la industria láctea permite una mejora organizativa que transforma tu empresa.
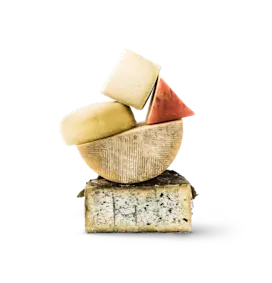