The Evolution of Maintenance
The Evolution of Maintenance
The Evolution of Maintenance
28 Mars 2018
Kay Jenkins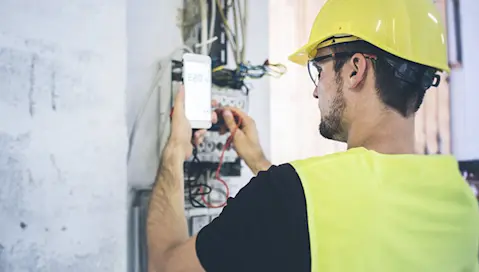
Maintenance has been around as long as humans have existed. From the routine sharpening of man’s earliest spears and tools to the repair work needed for modern technologies, our tools and machines have needed upkeep and repair. “If it isn’t broken, don’t fix it” is an adage that has been repeated for decades. But is that a viable approach in today’s plants? For the most part, the answer is no, especially when it comes to asset-intensive industries and smart factories. To illustrate that point, let’s consider three different maintenance strategies, when they’re effective and when they’re not – and how data can help improve them.
Reactive Maintenance
Reactive maintenance is the oldest strategy known to man: repairing or replacing a part after it has stopped functioning. This form of upkeep is responsible for 83% uptime in processes that use it exclusively. While that may sound good to some, what happens during the other 17% of the time? You can’t choose when a piece of equipment will stop working, and when downtime comes at inopportune moments, it can lead to a significant loss of time and money.
Preventive Maintenance
Preventive maintenance involves time or usage-based inspections and maintenance and typically is employed as an asset’s complexity increases. Preventive maintenance can increase uptime by as much as 5%, but can also lead to over-maintenance.
Proactive Maintenance
Observing patterns and trends in equipment operation and acting on signs that a machine will need some form of upkeep soon is the start of a more proactive approach to maintenance. In addition to longer life and lower costs, proactive approaches often align with organizational initiatives such as health and safety concerns, sustainability, and better regulatory compliance.
With Great Data Comes Great Opportunity
The types of maintenance we’ve discussed can be effective, but uptime can reach 98% when businesses begin to incorporate data into their maintenance strategies. With good data, a company can start to pinpoint why equipment failed, which provides an opportunity to intervene before failure in the future. The focus shifts from repairing to improving.
The goal for every organization should be to optimize its assets. Machines are getting smarter, finding patterns in data, and extrapolating generalizations from those patterns. Advanced strategies such as predictive forecasting and reliability-centered maintenance require a constant stream of data to improve equipment availability. The completeness, accuracy, and integrity of data becomes critical.
Are You Just Keeping Up?
Maintenance is being recognized as an area in which companies need to invest, rather than a cost to be reduced. To fully exploit the oceans of data generated by today’s assets, one of those investments should be an enterprise asset management system (EAM). And integrating it with your enterprise resource planning (ERP) system as well as your manufacturing execution system (MES) should be a top priority. This type of initiative is iterative and typically includes learning and continuous process improvement over a long period, so setting the right expectations among stakeholders is important. But that shouldn’t dissuade you from moving forward; instead, it should encourage you to begin now.
Ready to get started optimizing your assets and improving equipment availability? Contact us today to find out how.
Prêt à transformer votre entreprise ?
Nous avons les solutions EAM spécialisées dont vous avez besoin pour relever les défis de votre secteur.
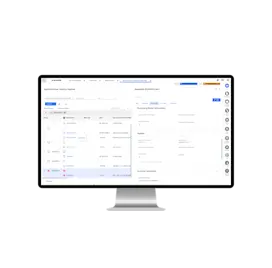