In diesem Beitrag vorgestellt
7 Ways to Step Up Apparel Production with Automation
7 Ways to Step Up Apparel Production with Automation
9 März 2023
Aptean Staff Writer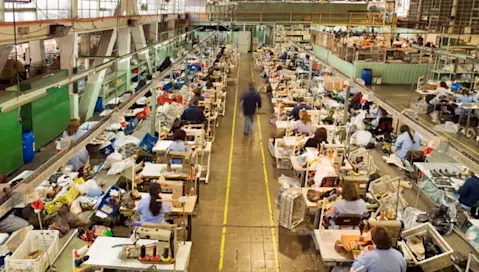
The fashion and apparel industry faces several challenges in 2023, including maintaining a competitive and cost-effective workforce while alleviating supply chain constraints. Our 2023 Fashion and Apparel Manufacturing Report for North America revealed challenges over the last year identified by fashion and apparel executives.
Their answers expressed these top four areas of concern:
Labor constraints with higher costs and higher turnover
Maintaining inventory and matching production schedules to availability
Supply chain pressures including rising costs
Winning new business and improving relationships
Our research found 42% of North American fashion and apparel manufacturers are facing staffing shortages—noting lack of skills and knowledge as their biggest barrier to 2023 business objectives. Fortunately, fashion-specific apparel automation can help apparel manufacturers scale up production while managing workforce challenges.
In fact, our apparel manufacturing survey showed 53% of apparel brands are already using technology to automate more tasks. Additionally, analysis by McKinsey & Company predicts brands that adopt digitally enabled value chain solutions could see a 50% reduction in time to market and a 20% decline in manufacturing costs.
So, where do you begin with your apparel automation?
ERP + Shop Floor Control = Organization-Wide Efficiency
What is enterprise resource planning (ERP) software? ERP software provides the core business management and operations hub of your organization. Data runs through an ERP seamlessly from one end of your business to the other. ERP systems streamline processes and automate reporting to drive financial management, purchasing, inventory management, vendor management and more. What is Shop Floor Control software? Shop Floor Control provides the execution layer of your manufacturing apparel automation. It enables increased productivity and efficiency on the manufacturing floor, giving production managers full visibility into bottlenecks and quality issues and providing valuable feedback to operators.
Aptean Apparel ERP and Aptean Apparel Shop Floor Control work together to provide a unified system and a single source of truth. Combined, these solutions offer seven ways to streamline operations, boost productivity and better utilize your skilled workforce.
of North American fashion and apparel manufacturers are facing staffing shortages
1. Gain Real-Time Visibility for Better Accountability, Forecasting and Decision Making
Our apparel ERP and shop floor control software collect real-time data and provide rapid, accurate reporting. This enables fashion and apparel brands and manufacturers to react more quickly to changing business conditions. Accountability: From top-level management right down to shop floor operators, real-time visibility helps your workforce become more accountable for their own productivity. At a management level, apparel automation helps you track and manage material costs and keep an eye on inventory costs. Aptean Apparel ERP helps managers make informed decisions with a customizable dashboard, report builder and 100+ out-of-the-box reports. Forecasting: Real-time information about inventory and orders leads to more accurate sales forecasts and production plans. Better reporting may enable you to pick up on changing consumer preferences earlier and adjust production plans to avoid stale inventory or stock-outs. Our apparel ERP can filter SKUs by size and color features to help you optimize inventory management and improve trend forecasting. Production Schedules: When you have high confidence in the accuracy and timeliness of inventory data, you can plan tighter production schedules and keep your lines running.
Hosiery manufacturer, Royce Too, switched to Aptean Apparel ERP to take advantage of a database built to handle apparel-specific data like colors, sizes and how many pairs make a retail unit. Leveraging the system’s easy reporting capabilities, warehouse management and ability to match shipping windows to inventory/production, Royce Too was able to reallocate 20% of employee time to more revenue impactful business areas.
2. Incentivize Productivity and Output
Shop floor control software can help production managers optimize operator performance to enhance production and meet deadlines. Aptean Apparel Shop Floor Control supports hourly or incentive pay models. You can apply incentive pay to individuals or teams and roll incentives out instantly—even in the middle of a production run—if deadlines are in danger of being missed. The system also supports different hourly rates based off labor skills. In this case, the same operator might earn a different rate when doing higher skilled tasks or using more specialized machines.
Data flowing out of our shop floor control system can help elevate trust for both operators and management by enhancing visibility. Management gains a better view of individual output, team productivity and even task efficiency by operator. At the same time, the real-time feedback operators receive about their productivity and compensation can help motivate them and establish trust that the system is capturing all of their work accurately.
Grand Forest Inc. manufactures chainsaw protective clothing and adopted both Aptean Apparel ERP and Aptean Apparel Shop Floor Control to increase productivity and efficiency. By automating tracking of production, inventory and incentive pay, Grand Forest reduced administrative time by 80% and achieved a 10% increase in shop floor productivity.
3. Match Operators With Tasks Based on Individual Efficiency
When orders have a tight production deadline, it is important to deploy your best operators in the most productive way. Our shop floor control system tracks the efficiency of each individual operator across individual tasks that operator has performed before enabling management to assign each person to the machines and tasks they perform most efficiently.
of apparel brands are using technology to automate more tasks
4. Pinpoint Quality Issues Quickly and Stop Them
Maintaining high quality is essential if you are trying to step up production. Problems with quality can result in wasted materials, reduced operator productivity—and in worst case scenarios—missed deliveries to customers. Apparel automation helps production managers catch quality issues more quickly and pinpoint the source of the problem for rapid remediation.
Integration with our apparel ERP ensures complete traceability, so if an end product has a quality problem, it can be traced right back through production stages. When a piece fails quality check, our shop floor control software registers a fault. You can trace back to the source of the problem—for example: a faulty machine requiring maintenance or an operator who needs additional training—then remediate the issue.
5. Identify and Remediate Manufacturing Bottlenecks
Shop floor control automation helps management analyze production and optimize operations—all in real-time. This powerful tool makes it easy to identify bottlenecks; before production hits a snag, reallocate operators or machines to rebalance the line and eliminate the bottleneck right away.
Workwear brand, Carhartt, implemented Aptean Apparel Shop Floor Control to enhance real-time visibility and gain flexibility in operator pay calculations. The system helped managers eliminate production bottlenecks, deploy individual and team incentives, increase average efficiency by 13% and redeploy three full-time payroll personnel toward more strategic work.
6. Save Time and Improve Accuracy by Reducing Paper and Manual Tasks
Across your organization, every single task you can automate will save time and improve the overall productivity of your workforce. Seamless integration between our apparel automation solutions sends data across the organization, so no one wastes time keying information from paper processes into multiple systems or importing spreadsheets.
Our shop floor control system replaces paper gum sheets with handheld scanners and a mobile tablet. It supports facial recognition so operators don’t spend time waiting to clock in. It sends operator and production data to our apparel ERP for use in payroll, inventory, order tracking and more.
U.S. Military and law enforcement apparel supplier, Propper International, leveraged Aptean Apparel Shop Floor Control to eliminate gum sheets and bundle tickets, saving 15 minutes per operator each day. The company saves an additional three to five hours each shift in production reporting and payroll calculations. Sewing operator efficiency increased 15% due to real-time feedback helping operators up their pace and boost their earnings.
7. Proactively Nurture Customer and Vendor Relationships
Stepping up production successfully means keeping promises to customers. Visibility into real-time data helps you improve your partnership with vendors to solve supply chain and production snags before they impact customer deliveries.
Aptean Apparel ERP includes a web-based vendor portal empowering seamless communication about product information and supply chain data. Communication remains within the system, so nothing gets lost in the back-and-forth of emails and spreadsheets.
By working more closely with vendors and staying on top of real-time inventory levels and production schedules, brands can communicate proactively with customers about order status and potential solutions if delays occur.
Additionally, EDI is built into the ERP system and is already connected to an extensive set of apparel retailers to facilitate fast, accurate exchange of data for further apparel automation.
Scale Manufacturing for Economic and Business Conditions
Specialized apparel-specific ERP and shop floor control make a winning combination for brands seeking the ability to scale production rapidly as business grows or the economy changes.
Real-time visibility and feedback help the workforce accomplish more while holding down costs. Operators are incentivized and empowered; management is better equipped with accurate inventory levels and production schedules. Relationships with vendors and customers are further strengthened as visibility enhances communication and problem solving.
Ready to learn more about stepping up production with Aptean Apparel ERP and Aptean Apparel Shop Floor Control? Ask for a demo to see the efficiency of integrated, fashion-specific automation.
Sind Sie bereit, Ihr Unternehmen grundlegend zu verändern?
Wir bieten Ihnen die spezialisierten MES-Lösungen, die Sie für die Herausforderungen Ihrer Branche benötigen.
