Aptean Apparel ERP, Exenta Edition and Aptean Apparel Shop Floor Control Case Study: Grand Forest, Inc.
Aptean Apparel ERP, Exenta Edition and Aptean Apparel Shop Floor Control Case Study: Grand Forest, Inc.
Aptean Apparel ERP, Exenta Edition and Aptean Apparel Shop Floor Control Case Study: Grand Forest, Inc.
20 Okt 2021
Überschrift
- Grand Forest, Inc. Gets Finished Goods to Customers Faster With Integrated Aptean Solutions
Grand Forest, Inc. is a premier manufacturer of chainsaw protective clothing and distributor of quality outdoor brands. The company can also be contracted to produce private-label products that adhere to a customer’s specifications.
Grand Forest owner and CEO, Carrie Bovender, believes that loggers should be safe and well-equipped at all times. As such, all of the company’s chainsaw protective apparel and rugged workwear is meticulously cut and sewn in its Summerville, South Carolina facility.
The Challenge
Grand Forest was running two standalone systems: an enterprise resource planning (ERP) system and a time and attendance package for tracking labor rates. The separate solutions didn’t provide the level of visibility the company needed in tracking product progress on the shop floor.
Didn’t have the real-time data or flexibility needed on the shop floor
Managers spent too much time on administrative tasks like ticket scanning and tracking for incentive pay
“Our previous ERP was a standalone system, so we had to manually integrate data from our time and attendance system. It wasn’t fluid at all,” Bovender recalled.
“Using an apparel-related ERP is key for any apparel or soft good manufacturing entity, because we have unique operational and administrative needs.”
The Solution
The Grand Forest team wanted a solution that provides greater visibility on the shop floor, real-time ERP integration and features designed specifically to meet the needs of apparel and soft goods manufacturers.
Aptean Apparel ERP and Aptean Shop Floor Control were the perfect systems to meet these criteria—providing an end-to-end solution, they embolden responsive supply chain operations, better informed decision-making, and increased sales and margins.
“While we looked at other systems, we choose Aptean Apparel ERP and Aptean Apparel Shop Floor Control because of the flexibility and the fit to our industry,” Bovender explained.
“Having an integrated ERP and shop floor system means we can get goods to our customers more quickly, because we know when something’s available to be shipped as soon as possible.”
The Results
The implementation of Aptean Apparel ERP and Shop Floor Control provided Grand Forest real-time visibility to track progress on the shop floor. With the new systems in place, customer service and management can see what products are being produced and when they’ll be available for shipping. Additionally, operators can record quality assurance checks on the floor and management can view real-time data about potential issues, including defects and repairs.
Improved inventory tracking
Reduced administrative time by 80%
Faster turnaround time
Improved employee experience and job satisfaction
Increased productivity by 10% in the first month
Grand Forest chose Aptean for the system’s flexibility and the ability to personalize each individual experience. In fact, each user can customize their screen and tablet interface which sped up implementation time, increased productivity, made employee tasks easier and improved job satisfaction.
“Aptean Apparel Shop Floor Control (SFC) is amazing. The interface is so clean and clear that it is easy to implement and adopt. Even the less tech savvy operators have embraced SFC easily and enjoy using it, which has translated into higher job satisfaction and increased productivity, so much so that Grand Forest achieved a 10% increase in productivity in the first month alone.” Bovender noted.
Because Aptean is focused on solutions for the unique needs and challenges of the fashion and apparel industry, Bovender is confident that Aptean Apparel ERP and Aptean Shop Floor Control will continue to grow with Grand Forest.
“Aptean not only understands apparel and soft goods manufacturing, but they also embrace it. They really understand how we’re moving things through a factory,” note Bovender. “More than anything, it’s clear that the team at Aptean really cares about Grand Forest and wants to see us succeed.”
“Aptean is a true partner, always looking for ways to help us improve and enhance our business. As we have grown, Aptean Apparel ERP and Aptean Shop Floor Control have grown with us.”
Ready To Cut Back Costs and Boost Growth With Aptean Apparel ERP?
With seamlessly connected apparel software systems, you can eliminate silos, streamline processes, improve supply chain management, reduce costs and boost productivity. In the fast-moving fashion and apparel industry these benefits unlock the next level of competitive edge.
If you’re ready to accelerate growth, Aptean is an ideal choice as our apparel experts have designed a full suite of solutions to solve your unique industry challenges. And our expertise doesn’t stop there. We pride ourselves on being a by-your-side partner through implementation and beyond—so our dedicated in-house teams are always on hand to ensure you’re getting the most out of your systems.
Discover more by checking our cloud-based apparel ERP, shop floor control software and product lifecycle management software.
Alternatively, request your personalized demo to see the software in action and understand how your business could benefit straight out of the box.
Sind Sie bereit, Ihr Unternehmen grundlegend zu verändern?
Wir bieten Ihnen die spezialisierten MES-Lösungen, die Sie für die Herausforderungen Ihrer Branche benötigen.
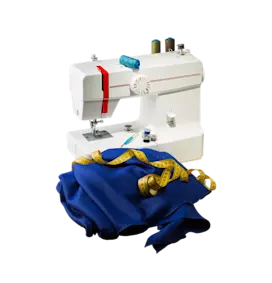