The Hidden Costs within Your Warehouse and How an ERP Can Help
The Hidden Costs within Your Warehouse and How an ERP Can Help
The Hidden Costs within Your Warehouse and How an ERP Can Help
27 May 2020
Ken Weygand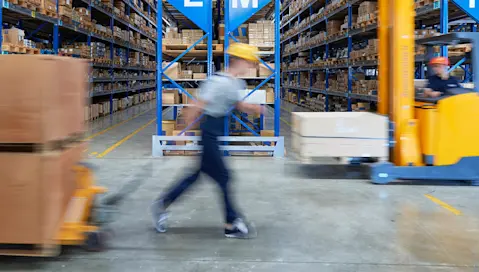
Let’s face it: warehousing should be relatively straightforward. Product is received, put away, picked and then shipped with an occasional count to ensure that everything is in order and that the customer will end up satisfied. But in between each of those steps are dozens of processes to ensure that the product does, in fact, end up in the right place at any given time.
The consequence of an inefficient and ineffective warehouse can be disastrous. If you can’t find the product, either to misplacement, improper order management or disorganization, then you can’t ship it. If it takes your warehouse staff longer to find an item than the customer paid for in labor costs, then your chance of a long-term profitable business is slim. Your business is the sum of all its parts, and unfortunately, the lowest common denominator usually thrives.
These days many companies have enterprise resource planning (ERP) solutions to help them manage all the departments and processes within their business, and between inventory management, inbound and outbound shipments, labor, tracking and accounting, it’s a lot to worry about. Most ERP solutions, however, do not offer the kind of functionality needed to effectively manage warehouses and distribution centers. Many businesses, then, turn to a separate warehouse management system (WMS) to support warehouse efficiency and streamline warehouse processes. But utilizing two disparate systems – a WMS and an ERP – to run your business adds complexity to your technology stack, increases overall costs and requires internal resources and time to implement the two systems and configure them correctly.
Instead, an industry-specific ERP with a built-in WMS may be the best solution for your company. Working together, an ERP and a WMS effectively control the movement and storage of materials within your warehouse, accurately track and streamline receiving, picking and shipping processes and then store all subsequent data for traceability and reporting purposes.
Without the use of an ERP with built-in WMS functionality, your company may be struggling to stay profitable. Hidden warehouse costs can have a major impact on your bottom line, customer satisfaction and the overall success of your business. Below, we outline four hidden warehouse costs that can be addressed with a WMS and how an ERP with WMS functionality will help your company improve efficiencies, streamline operations and manage growth.
Labor
Labor is the most expensive variable cost in any warehouse. No matter how well-organized your warehouse space is, or how many big-name customers you have or how intelligent your inventory tracking tools are, without a productive workforce, success will be challenging. A robust WMS that enables warehouse managers to actively engage, monitor and measure employees as they go about their shifts is an invaluable tool. While it’s fairly simple to track productive time (based on product input and output), it’s the labor involved in everything in between those tracked processes that could negatively impact your bottom line.
The right WMS allows supervisors to use real-time labor analytics to track and compare employee performance. Not only does this support business needs, but it encourages employees to perform their jobs to the best of their abilities. It makes employees accountable for their actions and workloads. If a shift is eight hours, those hours need to be spent productively, and with a robust WMS, you can track the jobs, movement and work of each employee.
The ability to issue alerts and notifications in real-time to workers in the warehouse is an extremely powerful tool - you can redirect staff, materials and equipment in response to changing demand requirements. And with the right WMS tools, the transition process is fluid, labor isn’t wasted and time is maximized.
Time
Travel time is virtually invisible and extremely expensive if allowed to go unchecked. Just as a manager would not want to see employees aimlessly wandering around, equipment should not be crossing the floor unloaded, or traveling to the far corners of the warehouse to pick the product when the same product is available within eyesight. The right WMS can provide three solutions to help resolve this issue.
Slotting is the placement of products within a warehouse facility. It maximizes a warehouse’s available cube space by improving storage and picking efficiency and reduces warehouse handling costs by optimizing product location and balancing workload. This strategy considers several factors – such as location, dimensions, and weight – to profile and sequence items down the pick path. Proper slotting leads to reduced picker travel, more stable loads, fewer accidents and less product breakage.
Interleaving is a practice in which the WMS assigns tasks to workers in ways that make use of each trip that they and their associated equipment make during each work shift. This practice typically can eliminate 25-30% of the machine travel associated with pallet moves.
Picking strategies are one of the easiest and most cost-effective ways to maximize productivity and improve order accuracy. The process of batch picking, for example, involves grouping multiple orders into small, consolidated batches. Using WMS tools to group orders together allows workers to optimize picks and increase pick density, which reduces the number of times a picker has to travel through the aisles. Another picking strategy, zone picking, divides the warehouse into multiple zones and assigns workers to pick only within one zone, reducing travel time. Orders are either picked and passed from zone to zone for fulfillment or consolidated at a point before shipping. A WMS automatically breaks apart the items needed based on the defined zones and will then give each picker exactly what and how many of each product they need to pick. This process would otherwise be very manual; a picker would look at the picklist which contains all items across all zones, and he/she would need to identify if there’s anything in their zone to pick, if so, pick it, and pass it to the next zone, and if not, simply pass it to the next zone.
Lastly, order picking, which is often the most preferred method of picking but not necessarily the most effective, includes picking one order at a time, following a route up and down each aisle until the entire order is picked. This method may work well in an operation with a low number of orders and a high number of picks per order; however, using this method in a warehouse with a large number of smaller orders would lead to excessive travel time.
Inventory
Inventory management is a balancing act. You don’t want to have too much inventory, which could lead to shelves filled with expired or obsolete products, expensive inventory holding or the need for a facility larger than what is really required. You don’t want too little inventory either, which could result in product shortages, unfulfilled orders and unhappy customers. In short, you need just the right amount of stock to effectively fill customer orders but to also stay as lean as possible. Companies can increase profitability 20-50% through careful inventory management.
Tracking inventory is essential. Product should be tracked and recorded during initial receipt, as inefficient practices at receiving could result in problems down the line. Whether it is through the use of bar codes or radio frequency identification (RFID), a detailed transaction history of inventory flowing in and out of the warehouse can improve visibility and reduce errors. Real-time data within your WMS means the system and the warehouse are never out of sync, ensuring better checks and balances with audits and cycle counts.
Shelf life and stock rotation can also have a major hidden cost implication. Warehouses need to know where each lot is stored and when and if the product is set to expire. Most warehouse management systems offer various controls to help manage the shipping of these products, such as last in first out (LIFO), first expiry first out (FEFO) and first in first out (FIFO). Without these controls, product can expire without ever being picked, and the costs associated with this are detrimental. There is the obvious cost of the manufacturing of these obsolete products, but also expensive warehouse space has been used to house the product and costly labor to receive and putaway the product can also be incurred with no payback.
Organization
The final area of hidden costs is the organization of the warehouse itself. Cost savings in travel time and inventory control can be lost if the warehouse is an incomprehensible maze. The first step is to determine how your facility will operate and develop a master strategy. Decide how space is used and think three-dimensionally (rather than expanding the footprint, for example, utilizing vertical space may be a better option). Examine potential traffic patterns and storage locations. Consider how items will be picked, how they will be put away and how the stock will be replenished. Group products into families based on the results of this analysis and configure your WMS to support this plan, building in exception protocols. Lastly, plan to work and work the plan. Without regular upkeep, a well-organized warehouse can quickly become disorganized and difficult to navigate.
Remember, warehouse efficiency shouldn’t be rocket science. It should be intuitive. Having a strong WMS will help reduce costs, increase inventory accuracy and storage capacity, and improve customer satisfaction. This will at least allow you to survive against your competitors. Using an ERP with built-in WMS functionality enables you to effectively manage all your processes and drive out those additional hidden costs, giving you a tangible advantage against your competitors.
If you want to talk more about how Aptean can help you and your business, reach out to us. We’d love to talk.
Ready to start transforming your business?
We’ve got the specialized WMS solutions you need to conquer your industry challenges.
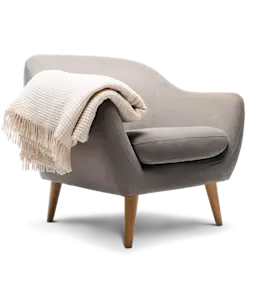