How Oil and Gas Companies Can Use Data to Become Best in Class
How Oil and Gas Companies Can Use Data to Become Best in Class
How Oil and Gas Companies Can Use Data to Become Best in Class
30 Ene 2019
Aptean Staff Writer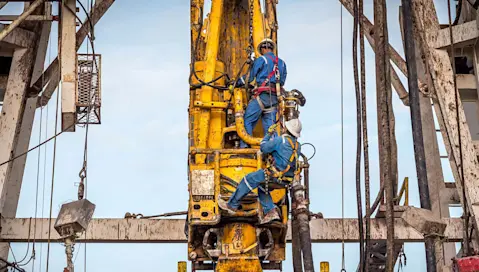
Selecting the right system is only the first step in becoming best in class. We shared a number of tips to help oil and gas companies navigate their way through the enterprise asset management (EAM) system buying process in a recent post.
What sets best in class oil and gas companies apart is their ability to make connections from their operational data and utilize it to predict future performance. Brad Charters, a leader in the oil and gas industry with more than 25 years of consulting experience, understands the importance of not only gathering data, but analyzing it appropriately.
“Oil and gas companies often lean on data to identify trends and highlight complex operational relationships. However, the data typically found in day-to-day tactical reports tell an incomplete story. An easy-to-use and robust analytics platform enables visualizations that pinpoint specific ways to define and measure the strategic goals that will drive profits. Imagine having the ability to create connections between your data across the organization, enabling you to anticipate the future performance of your business and assets. That knowledge has the power to fundamentally improve the way you operate.”
Becoming best in class requires an understanding of what metrics and KPIs are needed to get a full picture of how your operations have the potential to perform. To help you on this path, we’ve outlined three ways utilizing your oil and gas company’s upstream data can make you an industry leader.
#1. Real-Time Data Reduces Downtime
As a former Aptean TabWare user, Charters knew it was critical for his company to measure individual rig performance on a daily basis to get a full picture of the business’s operations. He integrated his company’s oil and gas EAM with its production management software and passed along those metrics to his executive team at their headquarters in Houston. The data allowed the leadership team to make decisions from hundreds of miles away. Charters’ company recorded unscheduled downtime well under the industry average.
“Production downtime equates to lost money on oil rigs and reducing it starts with understanding the downtime events that do occur and identifying the root cause. When you use analytics to see both sides of your operation in one integrated view, you will be able to uncover cause and effect relationships you may have never considered.”
Here’s an example: Production software records drilling at a site and, when integrated with your EAM, can help describe what is happening on a rig. By entering status event codes into your production system at set intervals, these codes indicate states such drilling, pumping, or waiting on cement. Pushing these codes into your EAM database and analyzing them with the maintenance data you already collect allows you to have a complete, all-encompassing view of your maintenance and production.
Being able to define, analyze, and solve for problems before they even occur is an enormous advantage for oil and gas companies. Having the ability to make operational decisions on a rig-by-rig basis with real-time, insightful analytics allows you to substantially minimize the risk of downtime occurring, resulting in significant impacts to your profit margins.
#2. Analytics Improves Rig Performance
A recent study found that rig culture is the main differentiator in driving high performance among employees. Promoting a healthy, safe work environment is a large part of creating a positive culture across your rigs, but so too is harnessing your analytics to develop a sense of internal competition to drive behavior and performance.
The phrase “A rising tide lifts all boats” is an excellent mantra to consider when it comes to instilling a culture of high performance across your rigs. By sharing rig and drilling data with your crew, you’re inevitably creating a sense of ownership over that data and over rig performance. This monitoring of company-wide metrics, as well as individual rig performance, encourages rig operators to compare themselves with other rigs and to try to understand how they can make small improvements to rise to the top.
Charters suggests implementing a self-find, “see something, say something” reporting process for your crew with the help of a system like an EAM. By putting this responsibility on your crew, you are positioning them as an integral part of the culture of operational excellence you are instilling across your rigs. Evaluating and analyzing adoption metrics of this process and making it available to all rig operators will continue to drive this friendly competition across rigs, keeping crews safe and further driving performance.
#3. Trend Analysis Promotes Proactive, not Reactive Maintenance
Part of Charters’ success in his former company was shifting the way his executive team thought about predictive maintenance. With the help of analytics, Charters was able to shift his company’s focus on addressing lagging indicators and instead anticipate and really understand leading indicators and act upon them based on real data.
“Collecting data from rig sensors provides even more reliable information that can be used for predictive maintenance. When conversations are taking place before any failure even occurs, operational efficiencies are multiplied.”
Analytics dashboards built into oil and gas CMMS or EAM systems provide a view into trends that may otherwise go unnoticed. An issue as small as a loose hose on a low-performing rig may be hard to detect if not for a dashboard that monitors production on a daily, weekly or monthly basis. With access to historical analytics and real-time data, a simple report or trend analysis showing that performance of that rig is dropping gives you the opportunity to address the issue well before it becomes catastrophic.
Don’t Just Gather Data – Analyze It
Becoming best in class begins with understanding your organization’s operations and the metrics and KPIs required to increase your lead over your competition. All the data in the world won’t help your business if you’re not analyzing it correctly. Utilizing your upstream analytics to reduce downtime, improve rig performance, and rely on leading, not lagging maintenance indicators will help you create a data-driven culture across your organization and become truly best in class.
Discover the key metrics and data management best practices you should consider for your oil and gas company, contact Aptean today.
Empieza a transformar tu empresa hoy mismo
Si estás listo para llevar tu negocio de producción industrial al siguiente nivel, nos encantaría ayudarte
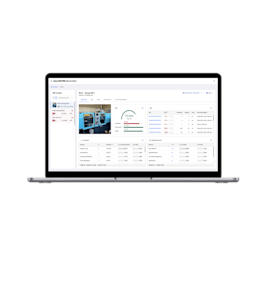