6 Reasons Your Food and Beverage Business Needs an Advanced Traceability Solution
6 Reasons Your Food and Beverage Business Needs an Advanced Traceability Solution
6 Reasons Your Food and Beverage Business Needs an Advanced Traceability Solution
19 Abr 2022
John McCurdy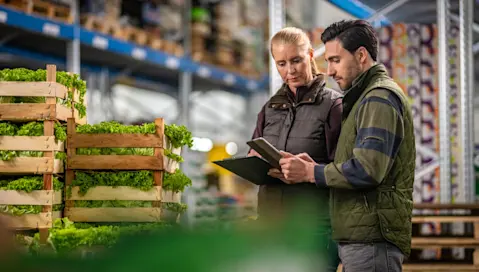
Many food and beverage businesses view good traceability practices as primarily a means of mitigating the financial risks that come with food safety emergencies and product recalls. This isn’t without reason, as the $10 million average cost for such incidents is no “drop in the bucket,” and additional research indicates that nearly a quarter of recalls cost even more—we’re talking $30 million.
That being said, preventing financial loss should not be the only motivating factor when it comes to putting a solid traceability system in place at your organization. There are many more benefits to reap from the right software, especially if it is part of an industry-specific enterprise resource planning (ERP) platform.
In this post, we’re going to take a look at six reasons for your company to adopt an advanced traceability solution beyond the obvious financial concerns. While all of the following goals come with monetary implications, each is worth pursuing in its own right and can help your business maintain and even gain ground as the market continues to evolve.
1. Maintain Total Visibility
The right traceability tools can help keep vital ingredient and product information highly visible and accessible no matter where the items are in your supply chain. The industry has moved beyond the “one step forward, one step back” paradigm originally created with the U.S.’s Bioterrorism Act of 2002, so your business really needs to have a comprehensive view from end to end.
And besides being able to keep tabs on movement of ingredients and finished goods, purpose-built traceability features of ERP systems also allow your employees to make decisions confidently based on the latest data. With a fully digital means of record-keeping, you’ll know that the information you have is accurate and up-to-date.
2. Automate Data Collection
A considerable advantage of food ERP platforms and the traceability functions they offer is their ability to automate the data collection process by integrating with smart equipment and connected devices. That includes handheld barcode and QR code scanners, which can efficiently capture information from data-rich labels to streamline your staff’s efforts.
Trusting to a digital means of data collection also eliminates the chance of human error, be it due to bad memory, messy handwriting or mistyping a figure. Removing those liabilities from your traceability processes goes a long way in establishing confidence and yielding actionable insights that can be executed upon with confidence.
3. Comply with Regulations
We mentioned the now-outdated provision of the Bioterrorism Act above, and while the standards for food traceability have grown more stringent in the intervening years, there’s even stronger regulations coming in the U.S. with the Proposed Rule for Traceability. Meanwhile, countries in the EU are subject to Regulation (EC) No. 178/2002 of the General Food Law, and its relatively rigorous set of rules helped member countries rank highly in a recent Global Food Traceability Center (GFTC) study.
By trusting to the traceability module of an award-winning offering like Aptean Food & Beverage ERP, you can protect your operations from the repercussions of falling short in this area, including fines from government agencies and even potential business closure. You’ll also be able to easily demonstrate accountability to any auditors who come to evaluate your traceability procedures.
For a complete breakdown of the different food traceability regulations around the world, check out this post.
is the average financial cost of a recall, but nearly a quarter cost $30 million or more
4. Communicate Transparently
When all of your material and product information is at your fingertips, conveying accurate information to consumers is a much simpler matter. And in addition to the traceability functions that give you immediate insight on critical details of the goods in your supply chain, ERP systems can automatically generate ingredient lists and flag allergens for proper declaration.
This sort of clear and straightforward disclosure on packaging and marketing materials also helps to establish good rapport with shoppers and encourage them to consider your offerings when they’re browsing the aisles of their local supermarket. Consider that a joint survey by FMI and NielsenIQ found that 72% of consumers said that transparency from food brands is “important” or “extremely important,” and you can understand just how crucial this measure can be.
5. Mitigate Food Safety Risks
We’ve already covered the financial risks of food safety emergencies, but a concern that could be just as vital to your future success is the damage to your brand reputation that such an incident could cause. The right traceability solution will help safeguard your organization from this threat by preventing contaminations before they occur and providing bidirectional tracking capabilities.
It's also a worthwhile goal in and of itself to better protect consumers from adverse outcomes by ensuring that your traceability systems are up to snuff. With a reduction as small as 1% in foodborne illnesses, more than 500,000 Americans would be spared getting sick each year, and that represents a massive opportunity for improving public health.
6. Streamline Recalls
Robust traceability features facilitate identifying the source of any contaminations in your supply chain and isolating the affected products and lots quickly. This is key, as time is of the essence when it comes to rectifying issues of food safety—beyond the financial outlays you might have to make should the problem go unchecked, you could also be risking the lives of vulnerable individuals.
ERP platforms built for businesses like yours can even expedite the process by automating certain steps in your recall procedure. While it would certainly be ideal to never have to deal with an emergency of this nature at your facilities, the fact that you can issue important notifications to partners and generate the necessary documentation with a few simple selections in the interface makes the situation more manageable.
Aptean: Your Partner for Tools to Tackle Traceability
We alluded to the superiority of our own Aptean Food & Beverage ERP earlier in this post, and while we might be a bit biased, there’s evidence to back up this claim. We have decades of collective knowledge and have successfully implemented our solution for more than 1,000 food and beverage businesses around the world operating across all subverticals.
Our friendly and highly qualified professionals can act as guides for your organization throughout the process of rolling out the software, including helping you to establish industry best practices and the steps necessary for excellent food product traceability procedures. We also understand flexibility is at a premium in a world rife with disruptions, so we encourage cloud deployments for clients who want that additional accessibility and agility for their critical systems.
Finally, there’s our outstanding reliability, with uptime of 99.9% or better guaranteed with our dedicated IT teams and redundant offsite servers. That means you’ll never be left wanting for critical traceability data when faced with an important decision with potentially huge business outcomes.
Now, if you’re ready to learn more about Aptean Food & Beverage ERP and its powerful traceability functions package, contact us today. We’re also happy to conduct a personalized demo so you can see the solution for yourself.
Empieza a aumentar la trazabilidad en tu operación
Si estás listo para llevar tu negocio de alimentos o bebidas al siguiente nivel, nos encantaría ayudarte.
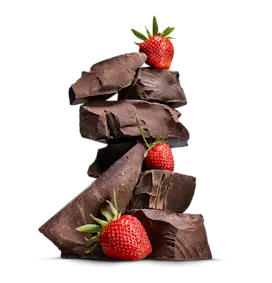