Discrete v Process Manufacturing ERP Software: What’s the Difference and Which Is Better?
Discrete v Process Manufacturing ERP Software: What’s the Difference and Which Is Better?
Discrete v Process Manufacturing ERP Software: What’s the Difference and Which Is Better?
17 Ago 2021
Daniel Erickson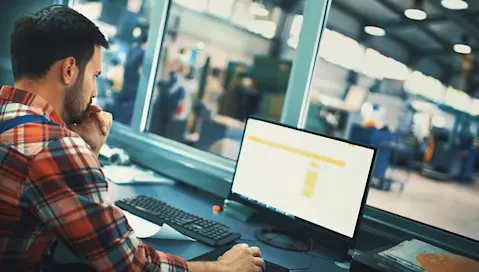
The biggest barrier to embracing new technology is not always understanding its value to your business; it’s knowing which software will deliver the GREATEST value. With so many options available on the market, it’s easy to become ‘choice blind.’
For process manufacturers, one major decision is whether to invest in a generic manufacturing ERP solution—or if specialized process manufacturing ERP software will yield greater value. With most organizations using their ERP software for 8-10 years before upgrading it, you want to find the right fit.
To find an ERP system that best supports your company’s processes, it’s important to appreciate how the differences between discrete and process manufacturing influence the way industry-specific software is made. And the specialized features available if you choose to go down the process manufacturing ERP route…
What’s the Difference Between Discrete and Process Manufacturing?
To understand why your choice of ERP software matters, look at the fundamental differences between how discrete and process manufacturing organizations operate.
Discrete manufacturing focuses on the creation of finished products for distribution or direct sale. These can be high volume products—such as electrical appliances and automotive vehicles—or complex, lower volume products such as agricultural machinery.
Either way, these manufactured goods contain components like nuts and bolts, which can be numbered, inventoried and tracked individually. A bill of materials (BOM) is used to identify the parts required and ensure identical construction on the assembly line. And if something goes wrong, the product can be disassembled and the component at fault located.
In process manufacturing, however, end products are created using a combination of raw materials or ingredients for industries such as pharmaceuticals, chemicals, food and beverage and cosmetics.
These ingredients need to be carefully measured as they’re manufactured in batches using recipes or formulas rather than BOM. And because they are blended or mixed together, raw materials cannot be returned to their original state. You can’t re-make tomatoes from marinara sauce.
What’s the Difference Between BOM vs Formulation/Recipe?
In discrete manufacturing, BOM provides the correct quantities of components, parts and raw materials, along with the assemblies and sub-assemblies needed to create the end product. This bill does not change from day-to-day.
With batch process manufacturing, however, calculating the formula is much more complex. Recipes can be updated or revised, attributes changes, proportions customized and volumes scaled. All this information needs to be captured for a full, compliant record of activity, and to deliver allergen and nutritional information. It’s not possible to deliver this sort of detail using BOM software.
Every day, the volume and proportion of ingredients needs to be calibrated in process manufacturing to reflect the size of the order. Industry-specific batch process manufacturing ERP technology can scale the quantities needed in order to create an accurate mix for every batch produced.
What Modules and Features Do You Get with Process Manufacturing ERP?
Process manufacturing ERP software combines the accuracy and flexibility needed for precision production. And it achieves this through three modules that aren’t typically available within generic manufacturing ERP software:
Recipe Management Careful formula control is critical to the quality and safety of process manufactured products. Choosing ERP software with a recipe management module enables your business to negotiate complex instructions, for a high-quality end result. Recipe management tools also capture valuable information batch-to-batch, such as revisions to the original recipe, the origin of raw ingredients, costings, by-products and co-products. Plus, you can use secure software logins to control who has permission to access proprietary recipe information.
Mixed Units of Measurement Accuracy is critical to process manufacturing, but the volume of goods you’re producing per batch may vary based on ingredient availability and customer demand. Batch process manufacturing ERP software allows you to manage different units of measurement for raw materials—for example, gallons and liters for liquids, and pounds or kilos for dry materials. And it can easily convert between standard and metric measurements, to ensure that recipes are of a consistent standard and ingredients maintain proportionality, however they are calculated.
Quality Control In addition to managing quantity and proportion of ingredients, the features of process manufacturing ERP software can help your organization to maintain quality control. Forward and backward lot traceability manages the shelf-life and expiration dates for perishable goods, ensuring consistent standards from batch-to-batch. From raw state through work in progress (WIP) to finished goods, using technology to coordinate quality control ensures complete accountability—and supports compliant manufacturing in line with industry regulations.
Why Does Choosing Process Manufacturing ERP Software Increase ROI?
While generic ERP software will deliver value, technology specific to process manufacturing generates greater ROI.
Why? Because choosing an ERP solution created for your type of manufacturing provides functionality that’s designed specifically to solve your industry challenges and streamline your batch processing procedures. From coordinating complex recipes and formulas, through managing mixed units of measure and thorough quality control via lot traceability.
We know because Aptean specializes in delivering industry-specific value. Aptean Process Manufacturing ERP manages your business end-to-end, with full manufacturing, inventory and financial integration. Our software solution is specifically designed to support process manufacturers in the cannabis, chemical, cosmetic and nutraceutical industries.
Contact us for your free Aptean Process Manufacturing ERP software demo to find out more.
¿Todo listo para transformar tu negocio?
Tenemos las soluciones ERP especializadas que necesitas para superar los desafíos de tu sector.
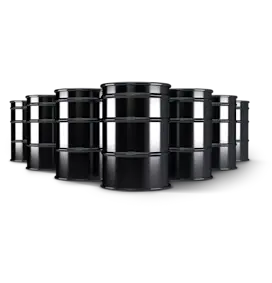