Destacado en este post
FAQs for Successful ERP Implementation in the Manufacturing Industry
FAQs for Successful ERP Implementation in the Manufacturing Industry
8 Mar 2022
Andy Pickard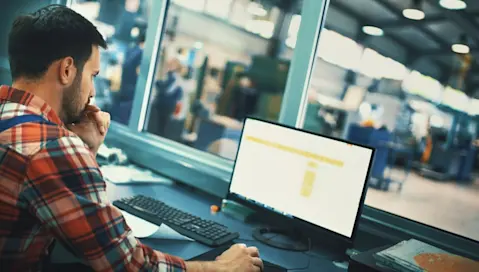
You’ve decided to upgrade your manufacturing ERP software. You’ve identified your business needs and found a technology vendor that can meet them. Now it’s time to deploy your new ERP solution.
That should be simple, right?
Not always…
It’s surprising how often an ERP implementation in the manufacturing industry is plagued by problems, because software providers and users haven’t aligned their expectations. To help you avoid falling into this group, here are some questions you should ask your vendor (and yourselves) once you’ve selected your preferred manufacturing ERP software.
Who’s Driving Your Manufacturing ERP Implementation?
Clear communication and a well-defined working structure will provide a solid foundation for successful ERP implementation in manufacturing. But to ensure this, you need to know who’s driving the project, internally and externally.
Before you start your new manufacturing ERP implementation, curate a dedicated deployment team and assign a project manager, who can work closely with your implementation team vendor-side.
Formalizing your task force will also enable you to set clear delivery expectations—for example, how frequently to expect project updates, and whether these updates will be delivered by email, phone/video call or in-person meeting (or a mix of all three methods).
Is Your Chosen Manufacturing ERP System Cloud-Based or On-Premise?
The time it takes to complete your manufacturing ERP implementation and the level of potential disruption to your business will be greatly impacted by the type of solution you select. So make sure you understand early-on how your chosen technology stack works.
For example, an on-premise ERP system needs to be installed on-site, with new hardware purchased up-front. This can result in an expensive, intensive implementation process. It also means that software engineers are likely to require a site visit for future maintenance, bug fixes and upgrades.
In contrast, cloud-based manufacturing ERP software is set-up remotely, for employees to use in any location with a Wi-Fi connection and web browser. With no on-site visits necessary, deployment times are often quicker with a cloud set-up, and the technology itself can be accessed by a wider number of employees. This is particularly important if you’re looking for a multi-site manufacturing ERP system, as choosing cloud-based technology can bring the cost of deployment down significantly.
Plus, with a cloud-based manufacturing ERP, your vendor’s technical support team will be able to patch problems and install software updates virtually—for a quicker, more cost-effective customer service.
For a full breakdown of the differences between on-prem and cloud ERP deployments as well as a comprehensive list of the pros and cons of each check out our full guide: The Real Difference Between On-Premise and Cloud ERP Solutions
What ERP Modules Are Included As Standard?
When you’re doing an ERP product demo, your technology provider will show you everything that the software can do. But some vendors will showcase features that aren’t available as standard, to encourage you to purchase add-ons.
Before you sign on the dotted line, make sure there’s complete transparency in your ERP software contract, so you gain access to all the critical modules your business requires.
The functions available to you may depend on the type of solution you select; for example, Aptean has dedicated industrial manufacturing ERP, process manufacturing ERP and food manufacturing ERP solutions, which contain different, tailored features for each sector.
If you’re not sure whether the ERP software you’re considering can fully deliver on your needs, our manufacturing ERP features checklist will help you find the right-fit solution. It’s always worth double checking before you start rolling it out.
Can Your Manufacturing ERP System Integrate With Other Business Software?
The powerful thing about manufacturing ERP software is its wide-ranging functionality. Your organization can use it for everything from materials requirement planning and inventory control, to compliance management, supplier management and order forecasting. And a sector-specific ERP system can also coordinate industry-specific elements such as formula/recipe calculations, allergen management and creating a Bill of Materials (BOM).
Many manufacturers choose to run all their business operations through their ERP software, because it’s simpler to manage and employees only have to learn one platform.
However, some organizations have complementary systems in place that they want to keep using alongside ERP. Or they decide to invest in niche solutions further down the line, to tackle targeted issues.
Talking to your vendor about integration capabilities will enable you to understand what’s possible for your current and future technology stack, and also factor-in the time and cost impact of connecting multiple platforms, depending on the complexity of the process.
How Long Will the Manufacturing ERP Implementation Process Take?
We’ve already mentioned some of the elements that can affect how the length of your manufacturing ERP implementation—from installing an on-site solution versus cloud software, to single/multi-site operations, and integrating third party systems. Every implementation is different.
That being said, there are ways to measure how long your ERP deployment is likely to take.
A well-organized technology vendor will have a clear deployment plan in place, with timings and deadlines accompanying each activity. And you can reap the benefits of putting an internal implementation team together by setting objectives and ensuring your software partner meets each milestone on-time.
Additionally, you can ask your chosen manufacturing ERP provider what work they’ve done with other manufacturers, using similar roll-outs as a benchmark for your own installation project. For example, when Grower’s Association, Fossa Eugenia, outgrew its previous ERP solution we were able to facilitate a quick turnaround to fuel the company’s continued fast growth.
Will Your Team Receive ERP Training?
Finding a manufacturing ERP system that meets your needs is critical to digital transformation and driving operational efficiency. However, any ERP investment needs to be utilized properly by your team to deliver its full value.
To make sure this happens, discuss employee training programs with your chosen ERP vendor to understand how your staff will get up to speed with new technology as quickly as possible. For example:
Do they lead the training program, or do they expect you to coach staff?
Do they run 1:1 or group training sessions?
Do they offer intensive courses or multiple modules?
Are their training schemes vendor taught or self-guided? Do they take place online or in-person?
Does your vendor offer ambassador/super user training programs for key people in your business?
Some manufacturing ERP vendors will have the flexibility to tailor staff training according to your business size and set-up, to impart knowledge in the most effective way possible.
What Ongoing Customer Support Will You Receive From Your Manufacturing ERP Vendor?
It’s not just initial training schemes that will drive manufacturing software ROI for your business. Inevitably, as new recruits join your company and you explore the full capabilities of your ERP system, there will be questions that need answering and issues that need troubleshooting.
Unfortunately, some manufacturers find out too late that their out-of-the-box software provider has limited follow-up customer services. And this results in their manufacturing ERP implementation not realizing its full potential.
To avoid this happening to your organization, discuss ongoing customer support with your chosen technology provider, so you can understand what’s available to your employees and whether there are additional costs involved.
How Long Will It Take To Start Seeing Results?
With a clear implementation and training program in place, it’s important that you set expectations for what your first few months using manufacturing ERP software will look like.
While some tasks and processes will be quicker and/or more efficient from day one, it may take longer to see the full spectrum of bottom-line improvements.
An ERP vendor with experience in manufacturing will be able to use previous customer encounters to benchmark success. For example, when The Metalworking Group implemented Aptean Industrial Manufacturing ERP, it increased on-time delivery rates to 86% (from 75%) within 12 months of onboarding the new software. And chemical manufacturer The Hammond Group reduced IT costs by 39% in the first year of upgrading to Aptean Process Manufacturing ERP software.
If your ERP software provider is able to share examples of their previous work, use these to create a set of realistic goals to measure your progress against.
What Data And Reports Can Your Manufacturing ERP Software Extract?
To set goals and benchmark success, it’s important that your manufacturing organization is able to extract, analyze and share data across your business. Particularly with senior leaders, who signed off on your ERP software investment but may not be using it day-to-day.
Choosing technology with built-in business intelligence features, like Aptean Manufacturing ERP, will enable every user in your business to access and report on the data they need to do their job better, and make stronger decisions.
And by using business intelligence features to validate the success of your ERP implementation, you can create a strong statistical business case for both expanding your current ERP use and investing in other manufacturing technologies.
Implementing manufacturing ERP software is a huge step towards your digital transformation goals and will help you achieve significant increases in visibility, efficiency, productivity and profitability. But, without the necessary preparation before and during the implementation process, the journey can easily become plagued with issues. By carefully selecting an experienced vendor and ensuring you answer all of the questions we described above, you’ll set your manufacturing business up for success from the start—and save yourself a lot of time and stress.
Looking for a technology vendor with a strong track record successfully implementing ERP software? Get in touch with Aptean to find out how we deploy market-leading manufacturing ERP solutions.
¿Todo listo para transformar tu negocio?
Tenemos el software especializado en tu sector que ayudará a tu organización a prosperar.
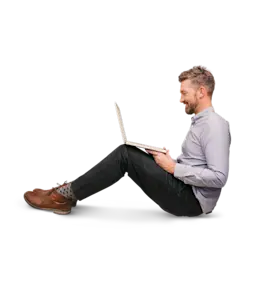