A Closer Look at 3 of the Largest Dairy Costing Challenges
A Closer Look at 3 of the Largest Dairy Costing Challenges
A Closer Look at 3 of the Largest Dairy Costing Challenges
Mar 26, 2020
Jack Payne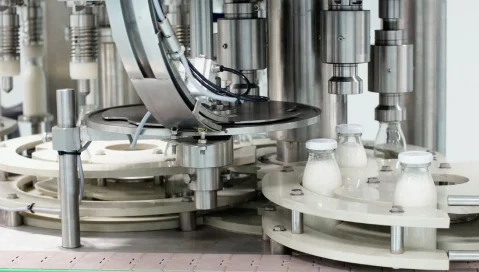
Dairy manufacturers undergo similar challenges across the industry when it comes to calculating dairy costs. How often do you consider the separate components of each glass of milk you drink? This is exactly what dairy manufacturers need to do when it comes to calculating costs.
Currently, dairy costing has provided companies with three main problems – managing costs by components, managing class of milk from the same supply, and not knowing what they will pay until after a month’s end. While these challenges are similar across multiple companies, how the companies decide to combat them falls into several different categories.
Managing Costs by Components
Each lot of milk that received from either the same dairy or different dairy varies in the component make-up; this is the percentage of butterfat, protein, solids, non-fat and other components or properties of the raw milk. The value of the milk is based on the percentages of each component in each lot with a higher value for more butterfat and more protein, and a lower value for less butterfat and less protein. However when raw milk is received is it generally received based on the weight of raw milk and not the components, as the components are properties of the milk received. This provides dairy producers with the challenge of measuring those components, specifically percentage of protein, percentage of butterfat and nonfat solids, in order to better understand the composition and value of milk in their silos. All milk is not the same in composition, so the solution is to track the inventory by weight, volume, and components in order to better value each receipt.
Managing Class of Milk
Domestically, dairy companies deal with the regulatory challenge of managing multiple milk classes based on the product produced from the milk, ranging from liquid milk to soft cheese, hard cheese and powders. When farmers send their milk supply to a facility that produces multiple milk classes, it is not known yet what class of product will be produced. The facility still needs to assign a class of milk to that supply, so usually, the lowest class that the facility produces is assigned until the class can be determined. Once the class is determined, the company must add a “class adder” for each component that makes up the differences between the product that will be produced and the unclassed raw milk initially sent over. This process is a huge asset for a better understanding of their monthly spending.
Not Knowing Payment until Month’s End
Finally, dairy manufacturers have difficulty reconciling what they’ll pay. Manufacturers receive estimated advanced pricing at the beginning of the month, but the announced price doesn’t surface until the following month. The final cost of manufacturing milk is determined by government regulations, and although projections have become more accurate, it is difficult to estimate what your costs will be until the final cost is announced. This leads manufacturers to deal with discrepancies later using other business transactions. These costing complexities within dairy manufacturing are what lead many organizations to make the move to a system that helps combat those challenges.
Many companies have discovered their own ways to manage these costing challenges. Many have turned to spreadsheets because of their flexibility. Often times, this option is achieved with smaller dairy manufacturers but can be error-prone. In the long run, the complexity of dairy costing begins to poke holes in this seemingly manual solution. Multiple spreadsheets with different versions among the team can become overwhelming, links become broken, security reliability becomes a concern, and data can be changed by multiple users, making this solution less attractive as your company grows.
A more attractive solution for dairy manufacturers is an ERP that specializes in dairy manufacturing and costing. This option has continued to grow in popularity because it provides dairy companies with a solution that supports their business growth by offering users more accurate real-time information through an application developed by a team with an understanding of the challenges within the dairy industry.
We understand that comfort is key, and people do not always want to embrace new changes, especially if the solution completely transforms the status quo. Even though change is hard, it can be for the best. And no solution is as flexible, robust, or thorough as an Aptean Food and Beverage ERP for dairies.
Our purpose-built ERPs provide you with the specific product and functionality needed, such as dairy costing, pooling, and detail lot characteristic tracking, to grow with your business. We help our customers reduce costs, increase efficiency, and provide industry compliance. Our expertise within the dairy industry allows us to quickly identify and support your unique business needs. When choosing an industry-specific food and beverage ERP solution like Aptean Food & Beverage ERP, you will receive ready-made functionality for all aspects of the food and beverage industry. Complicated processes call for advanced technology, so choose a solution ready to give you an all-in-one resource.
Ready to learn more about how an Aptean Food and Beverage ERP can support your business? Reach out today.
Ready for industry-specific solutions that unlock results?
Our specialized dairy ERP system enables organizational improvement that transforms your business.
