How Dairy Manufacturing Software Improves Your Production Processes
How Dairy Manufacturing Software Improves Your Production Processes
How Dairy Manufacturing Software Improves Your Production Processes
Aug 9, 2022
Jack Payne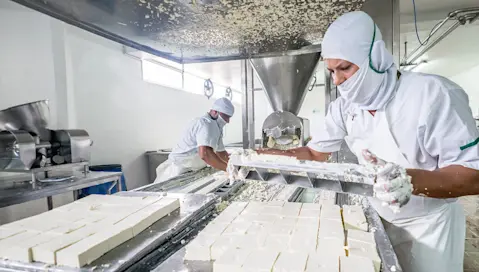
The cream in your morning coffee, the milk you pour over your bowl of cereal, the slice of cheese that tops your sandwich—for the average consumer, these all seem like pretty simple and straightforward products. Being a dairy industry professional, however, you know better.
You know that each lot of raw milk you receive is different and your production processes involve highly complex and exacting procedures. There are several challenges that are unique to your sector, and achieving success in the competitive and fast-paced food and beverage marketplace requires effectively overcoming them.
Thankfully, though, you and your teams don’t have to tackle these issues with nothing but your wits to serve you. There’s purpose-built technology designed for organizations like yours, and it comes in the form of dairy manufacturing software—specifically, that of the enterprise resource planning (ERP) variety.
Let’s dive in and examine just how these solutions can serve your dairy business by improving production processes as you approach key dairy developments and more.
Equipment Integrations to Streamline Component Analysis
Because the milk that cows produce varies based on the animal’s diet and other circumstantial factors, each lot you receive from your suppliers will have its own unique component breakdown. It’s crucial that you’re able to analyze it accurately and quickly, as the percentages of solids, butterfat, protein and non-fat will determine not only the class of the milk but also what products it’s best suited for.
Dairy manufacturing software can integrate with your electronic component analysis equipment to automatically import the data generated to your system, giving you an up-to-date look at just what you have on hand and allowing you to prepare for production. What’s more, advanced systems like Aptean’s dairy ERP allow for “class adding” to properly categorize the lots you receive and designate them for incorporation in the appropriate product line.
Robust Recipe Controls for Multiple End Products
Dairy companies like yours more often than not have several end products in your brand lineup. Between liquid milk, cream, butter, yogurt and cheese, you may be juggling many different finished goods in the production process, and each has its own precise parameters and expectations for taste and consistency.
That’s why you need the complete recipe and formula features offered by modern dairy manufacturing software. By giving your staff complete visibility and control over the amounts of the various ingredients used in your items and the ability to tweak when necessary, an ERP built for dairies can help you ensure that everything that comes off your lines meets the internal standards you set and the expectations your clients hold.
Bidirectional Traceability that Ensures Necessary Visibility
Traceability is an imperative in the food and beverage world, especially with the increased focus on public health that has developed in recent years. You need to be able to quickly determine what lots of raw milk were used in which products you’ve manufactured, as well as which suppliers provided those lots and where the finished goods ended up downstream.
This is just one of the functions in which ERP technology excels, and a platform designed specifically for dairy operations like yours will even be able to take into account the fact that multiple lots from different providers are frequently used in a single production run. That gives you peace of mind should a contamination or other food safety issue be discovered, as you’ll be able to quickly drill down and isolate both the source as well as the affected items.
Inventory and Expiration Management for Assured Freshness
Just as every lot of milk has a different component breakdown, so too does each have a different window of freshness and expiration date. With your supplies likely coming from multiple different providers, that’s a lot of information to track—and on top of that, it’s in your organization’s best interest both financially and from a sustainability standpoint to make the most of what you have and minimize waste due to spoilage.
Good dairy manufacturing software again has you covered, as an industry-specific system will allow for the automatic logging of freshness ranges as soon as your lots are received. A fully-fledged dairy ERP solution will automatically track all critical dates and trigger alerts when windows for safe use are closing, helping you put raw materials to use before it’s too late and ensuring all your products are safe to consume.
Financial Tools to Account for Costing Complexities
In the U.S., the federal government determines the exact prices for the different classes of milk at the end of each month according to various market factors. That means that dairy manufacturers like you can only work off cost estimates provided at the beginning of the month when conducting purchasing and financial calculations, which leads to undesirable uncertainty for your accounting department.
While historically businesses in the dairy sector have attempted to circumvent this issue by attributing differences between estimates and final costs to other transactions, the smart move is to use ERP software for dairy manufacturers to easily identify discrepancies and rectify them. These systems provide financial tools that are integrated with all other areas of operations, giving you a “single source of truth” for monetary matters—and all other important information, too.
Unlocking Better Results with an Aptean ERP
Here, we’ve focused primarily on the features of dairy ERPs that address the unique challenges of the sector, but there are additional benefits of such software that would serve any food and beverage business well. For example, a dedicated quality assurance module can automate important checks for greater efficiency and prompt employees with on-screen alerts when intervention is necessary.
ERP systems also offer production planning and demand forecasting tools that help you prepare for the future, including any changes in demand due to shifting consumer preferences or marketplace disruptions. What’s more, there are functionalities that will help your marketing and compliance professionals dial in your packaging and labeling requirements for optimal results.
Aptean’s ERP for dairy manufacturers comes with the additional benefits of the option for cloud hosting on a software as a service (SaaS) model and industry-specific technology built on the Microsoft Dynamics 365 Business Central platform. With this kind of powerful, cutting-edge technology on hand, you’ll be equipped and ready for whatever the future may bring.
Now, if you’re eager to hear more about Aptean’s dairy ERP solution and how it can improve your production processes, contact us today. You can also request a personalized demo.
Ready for industry-specific solutions that unlock results?
Our specialized dairy ERP system enables organizational improvement that transforms your business.
