Featured in this post
Excelling in End-to-End Food Logistics With Industry-Tailored Technology
Excelling in End-to-End Food Logistics With Industry-Tailored Technology
6 Mar 2024
John McCurdy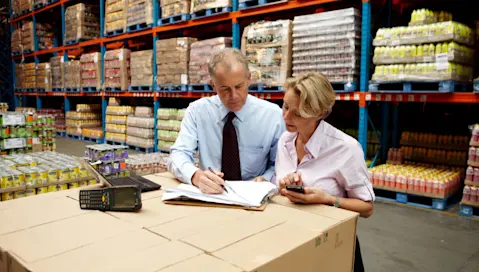
The everyday consumer can afford to be more or less blind to the intricate workings of food supply chains. After all, when getting all you need is as easy as making a trip to the local grocery or filling out an order for delivery, why should one fret about the particulars of how any given product ended up on a shelf or online storefront?
But for you as a food industry professional, the challenges of food logistics are very real and present issues that your business must overcome. With all the special considerations that come with your goods—not to mention the sprawling and splintered nature of modern distribution networks—getting things “from Point A to Point B” isn’t so simple as it sounds.
That said, it’s obviously vital for your organization to be able to reliably procure the products you need—be they ingredients for manufacturing or finished goods for distribution—and then deliver orders on time and in full. Thankfully, food supply chain software (or food logistics software) facilitates effective end-to-end management.
In this post, we’ll take a closer look at the features that today’s advanced solutions offer to help you keep the pipeline flowing, your customers happy and your bottom line robust. But first, we’ll go over the complexities that food logistics presents so that you can better understand how technology can be applied to successfully navigate them.
The Challenges of Food Logistics
Food logistics—which encompasses both the transportation and storage of products—is challenging due to a variety of compounding factors. Some of them stem from inherent qualities of food products, others are reflective of the market, and still others have only recently become serious concerns in supply chain management.
1. Traceability
Being able to track and trace products and their associated data both backward and forward along the supply chain is critical for two primary reasons. For one, it’s a matter of food safety. After all, if you don’t know where your materials came from and your finished goods ended up, you can’t isolate the source of a contamination or recall affected items.
In addition, ensuring compliance with food traceability regulations is imperative in virtually all jurisdictions, though the degree of transparency and thoroughness of record-keeping required varies. That said, the global trend is toward greater visibility into the movement of products, and enforcement agencies can levy heavy fees or force closure for violations.
2. Perishability
Unfortunately, foods and beverages don’t remain viable forever. Some can become compromised outside of ideal conditions, and many have short shelf lives. You must plan ahead with these considerations in mind, as otherwise you could end up with spoiled items—resulting in food waste and erosion of your profit margins.
Food and beverage businesses sometimes try to combat the problem of perishability with just-in-time (JIT) delivery, but that strategy has showed its flaws in an era of material scarcities and supply chain issues (which we’ll explore in greater detail later). To succeed, you need an approach that’s more adaptable and reliable.
3. Variable Demand
Whether it’s due to a surge in general popularity of a variety or a specific item, or the passing of seasons bringing back favorites at certain times of year, demand can change quickly in the food and beverage industry. If you can’t anticipate, monitor and quickly adjust to these shifts, you risk losing market share to your competitors that can.
The financial ramifications of not being able to account for variable and seasonal demand changes can be serious, as products that fall out of favor when something more enticing comes along—as well as seasonal products past their time of year—typically must be sold at a steep discount or otherwise liquidated, often resulting in a loss.
4. Customer Requirements
For food manufacturers, as well as dedicated food distributors, meeting the expectations of customers isn’t just about quality control. The requirements of retailers and foodservice outlets can be quite specific and sometimes difficult to satisfy, but not doing so could mean delivery failures, fines or a loss of business.
From electronic data interchange (EDI) for transactions to making sure the right kind of truck is sent according to the specifications of a client’s loading dock, there are plenty of considerations you’ll have to make, and even more customer rules to accommodate. That demands a detail-oriented approach that’s tough to implement without a good system.
5. Emergent Disruptions
Food logistics was tough enough before the pandemic drastically shifted consumer patterns and exposed the weaknesses of our supply chains. While the world has by and large returned to “normal,” smooth movement of goods along the pipeline is not a given, as transportation delays, material shortages and staffing issues persist.
If you can’t react with agility to changing circumstances that complicate the processes of obtaining materials and fulfilling customers’ orders, your bottom line is at stake. That reality demands that you employ a flexible approach to supply chain management and provide your employees with the tools they need to maximize their impact.
How Technology Facilitates Food Logistics, Every Step of the Way
So, what’s a food logistics manager meant to do in the face of such significant challenges, all bearing down at the same time? You need immediate high-level visibility of critical data to make your best decisions, but there are several critical steps that require attention at a more granular level. Enter food supply chain software as the solution.
1. Procurement
At this initial step of the supply chain, you must be able to transact with your suppliers conveniently, add new vendors as necessary, accurately predict your material needs, track inbound products and verify them at receipt. A food ERP can act as your “single source of truth” for all supplier information, but that’s just the beginning of its utility.
These systems also offer vendor item catalog functionalities that make it easy to purchase replenishments and track your orders, as well as forecasting tools that allow you to get a reliable estimate of what your material requirements will be. Meanwhile, inspection status and quality control features ensure that the proper checks are made at receiving.
2. Warehousing
After you receive your supplies, they’ll spend at least some time in your inventory. That means that you must have the means to not only update stock levels and maintain product details (including traceability data) but also monitor windows of freshness and ensure timely use of materials. A purpose-built food ERP can give you all that, and more.
The lot and sublot management tools of such a system give you item-level visibility to track goods as they move through your facilities, and the product specifications features allow you to capture vital information. Meanwhile, the expiration management functionality automatically deploys alerts when products are nearing the end of their viability.
3. Route Planning
Now we fast-forward through the processing and manufacturing phases to reach the next step in food logistics, route planning—where the goals are keeping costs down and operating within any restrictions. A food distribution ERP is the go-to in supply chain management up to this point, at which route planning software takes the lead.
Also known as route optimization software, this system can create optimal routes automatically in a fraction of the time it would take to do manually. An advanced algorithm accounts for driver hours, customer rules, compliance and other factors to deliver a plan that satisfies all requirements while minimizing mileage and vehicle wear-and-tear.
4. Execution
Once your drivers are on the road, you’ll want to monitor their trips and the storage conditions in their vehicles to make sure items aren’t at risk of spoiling. Luckily, routing and scheduling software affords you live execution tracking tools and allows you to set temperature-controlled zones in the cargo area to ensure safe transport of perishables.
Then, for the last mile, there’s electronic proof of delivery (ePOD) software that enables your drivers to easily collect photographs and signatures on a mobile device. By eliminating paperwork, this solution can increase accuracy and first-time delivery success rate while also providing customers visibility via ETA updates and confirmation emails.
5. Continuous Improvement
Successful food and beverage business leaders are always looking for ways to get better, so it’s only natural that routing optimization software offers dedicated continuous improvement features. By linking with GPS and telematics systems, the solution collects data on driver behavior and deviations from planned routes to inform corrective action.
At a higher level, the strategic route planning functionality of advanced routing and scheduling systems enables “what-if” scenario modeling to gauge the likely impact of making changes like adding trucks to the fleet or opening a new depot. That way, you can find the best way to achieve your goals within your means before incurring any expenses.
Finding the Right Provider for Your Food Logistics Technology
Food logistics is no doubt a difficult area of operations to master, but as you’ve learned, tailored industry solutions can provide you with the tools you need to excel on this front. That said, you know that a complete food supply chain software setup comprises multiple systems, and there are countless options to choose from for each.
As you consider the different alternatives, keep an eye out for vendors that can provide more than one of the solutions you need, as that will simplify your search and ensure greater interconnectivity in your tech stack. You also want to ensure that you choose a provider with a strong track record and deep expertise in the food and beverage industry.
Aptean’s dedicated professionals have decades of collective experience in the market and understand the best practices for applying technology to overcome the challenges of food logistics. We’re also dedicated to serving as a partner for each of our clients, helping to create a roadmap for implementation and further additions to your digital foundation.
What’s more, we can be the one-stop-shop you’re looking for to get a cohesive and integrated platform with comprehensive food supply chain management functionality. Plus, our award-winning food and beverage ERP, advanced route optimization software and ePOD solution are all available via the cloud to maximize your flexibility and security.
Want to learn more? Explore how a cloud-based ERP for food and beverage businesses can improve supply chain resilience.
Start increasing traceability in your operation
If you’re ready to take your food or beverage business to the next level, we’d love to help.
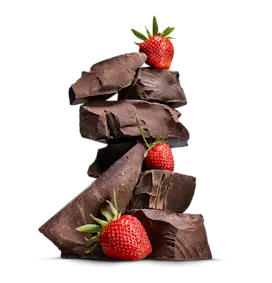