Revealed: Key Manufacturing Industry and Technology Trends for North America in 2025
Revealed: Key Manufacturing Industry and Technology Trends for North America in 2025
Revealed: Key Manufacturing Industry and Technology Trends for North America in 2025
Dec 23, 2024
Aptean Staff Writer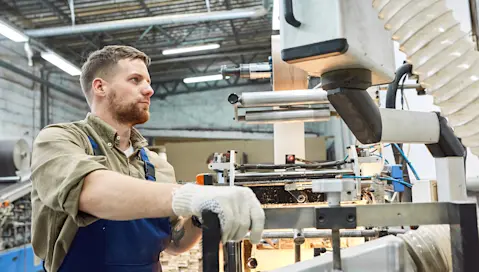
Today's manufacturers face mounting pressure to modernize their operations while dealing with persistent challenges like workforce shortages, rising operating costs and changing customer demands. The pressure to adopt new technologies is particularly acute, as companies seek to stay competitive in an increasingly digital landscape.
How can your manufacturing business navigate these challenges and position itself for growth in 2025?
To guide your strategic planning, we commissioned B2B International to conduct extensive research, including a survey of manufacturing leaders across North America. Below, we've highlighted five key trends that emerged from our findings.
This is just a preview of the full Manufacturing Industry Trends and Technology Report. Download the complete report for free to access all our insights.
Trend No. 1: Manufacturers Feel Pressure To Adopt New Technologies
Second only to rising inflation and material prices, the push to embrace emerging technologies topped the list of manufacturers' concerns for 2025. Nearly a quarter (24%) of respondents rate technology pressures as a "significant concern."
In response, 52% of manufacturers plan to implement emerging technologies and data solutions in 2025, while 48% aim to update or integrate their legacy systems.
Midsize companies are particularly keen to embrace automation, with 60% planning to adopt new technologies compared to 50% of larger companies and 42% of small businesses. This finding suggests that mid-market organizations see technology adoption as key to driving growth and competing effectively.
Trend No. 2: Digital Innovation Is Driving Operational Efficiency
Our research found that optimizing inventory levels and improving equipment performance are the top challenges that manufacturers want to solve with technology in 2025. The data reveals significant opportunities for improvement: Nearly half (49%) of manufacturers say their inventory management processes are still partly or completely manual, while 58% are still using partly or wholly manual processes for managing and monitoring equipment performance and servicing.
The commercial impact of digital transformation is clear, as companies already using software are generating higher revenue than those still reliant on manual processes. According to the data, the most pronounced financial advantage can be produced by utilizing enterprise asset management (EAM) software, but electronic data interchange (EDI), enterprise resource planning (ERP) and product lifecycle management (PLM)solutions also make a positive difference for businesses’ bottom lines.
Migration to cloud software is another trending development, with 66% of survey respondents indicating that their organization is either in the process or has already moved its ERP to the cloud. This also correlates with higher revenue growth, as those that have made the transition saw a 10.5% increase in 2024, compared to just a 9.6% increase among those still using on-prem setups.
Trend No. 3: Automation Is Key To Addressing Workforce Challenges
With 506,000 manufacturing job openings in August 2024 alone and The Manufacturing Institute predicting 1.9 million unfilled roles by 2034, digital transformation has become critical for maintaining productivity and making the most of existing human resources.
Automation is the most popular strategy to combat workforce challenges, with 63% of manufacturers using technology to automate more tasks, and an additional 30% planning to implement more automation via software in 2025.
This is proving an effective tactic, as manufacturers that increased automation in response to staffing and skills shortages grew their revenue by 9.6% on average in 2023-24, compared to 7.1% among those that took no action.
Currently, the most commonly automated tasks are managing production processes and volumes (55% mostly/completely automated) and tracking inventory (52% mostly/completely automated). On the opposite end of the spectrum, a third (32%) say their quoting and estimating process is still mostly or completely manual, while 29% rely on manual reporting and analysis.
Trend No. 4: Industry-Specific Solutions Generate Higher Revenue
Manufacturers using industry-specific technology are consistently outperforming those using horizontal software when it comes to revenue generation. For example, manufacturers using industry-specific business intelligence (BI) software generated 9.7% revenue growth in 2023-24, compared to 8.4% among organizations using horizontal software and 6.6% among those using homegrown solutions.
Industry-specific ERPs are also increasingly popular, with the main drivers for purchase being the limited scalability of existing solutions (47%) and the inability to meet customer demands with a dated tech stack (44%). These specialized systems provide a competitive advantage because they have built-in functionality for manufacturing processes—such as level one traceability for industrial manufacturers—reducing the need for costly customizations.
What’s more, ERP solutions tailored to manufacturers’ unique needs support compliance with industry regulations and the consolidation of data, both of which are critical for smooth day-to-day operations. Users also benefit from specialist vendors' deep industry expertise to generate faster time to value.
Trend No. 5: AI Adoption Is Accelerating
Artificial intelligence (AI) has moved beyond experimental stages and is delivering real-world impact for early adopters.Not only are 27% of manufacturers already using AI tools and another 44% in the process of implementing AI capabilities, but those implementing AI grew their revenue and profit by 9.1% on average in 2024, compared to 7.3% revenue growth and 7.6% profit growth among manufacturers not exploring AI.
The top benefits cited for using AI include improved efficiency, productivity and quality. However, perspectives vary by role. Operations and supply chain leaders are focused on using AI to reduce operational costs, while IT leaders prioritize insight generation, and executive management want AI to enable faster, more accurate data analysis.
Meanwhile, the biggest barriers to AI adoption are the complexity of the technology, high implementation/maintenance costs and data privacy/security concerns. As the technology becomes more commonplace, approachable and affordable, usage will likely increase given the potential advantages.
Shape Your Manufacturing Technology Strategy for 2025
These five trends paint a clear picture: Technology adoption and optimization will be crucial differentiators for manufacturers in 2025 and beyond.
To maintain competitiveness, your organization should prioritize industry-specific solutions that can deliver measurable improvements in quality, efficiency and automation capabilities, while building the foundation for advanced technologies like AI.
Ready to dive deeper into the future of manufacturing? Download the full 2025 Manufacturing Industry Trends and Technology Report. To learn more about Aptean's industry-specific manufacturing solutions, contact us or request a personalized demo.
Request a callback from a manufacturing ERP expert
Discover the benefits of software designed specifically for the discrete manufacturing industry.
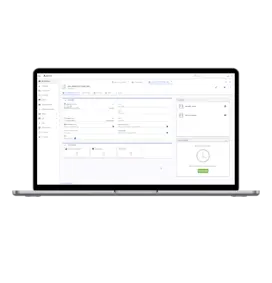