En vedette dans cet article
Starting Your Digital Transformation in the Food and Beverage Industry With Purpose-Built Software
Starting Your Digital Transformation in the Food and Beverage Industry With Purpose-Built Software
20 Oct 2023
Aptean Staff Writer
A recent study revealed that 42% of food and beverage companies are concerned with surging inflation rates and higher material prices. The solution to these challenges: automation. Those who embraced automation saw a whopping 20% higher growth rate compared to companies still using manual, paper-based processes.
Indeed, the food and beverage industry is in the midst of an urgent and imperative digital transformation with 48% of companies gearing up to automate more processes in 2024 per the same study. To achieve the best results on your journey to digital transformation and automation, you'll need industry-specific software solutions designed for your challenges and developed by professionals with in-depth market knowledge.
In this blog, we’ll talk about how the manufacturing trifecta—enterprise resource planning (ERP), enterprise asset management (EAM) and overall equipment effectiveness (OEE) software—can accelerate the growth of your operations. We’ll also highlight the remarkable synergies you can unlock by integrating these solutions and forming a cohesive tech stack from a trusted provider.
Seamless Integration of Food and Beverage Manufacturing Software
ERP, EAM and OEE are complementary systems that can work together to provide a holistic and integrated approach to your food and beverage manufacturing operations. By integrating these solutions, you can leverage the data and insights from each solution to improve your decision making, planning and execution.
The main benefit of integrating ERP, EAM and OEE is achieving comprehensive operational excellence. Together, these solutions can produce real-time insights into resources, assets and performance to drive success. Such an integration can help position your business at the forefront of Industry 4.0, ultimately accelerating your growth in the ever-evolving food and beverage landscape.
Now, let's take a closer look at each system to understand how they work for your manufacturing operations.
Those who embraced automation saw a whopping 20% higher growth rate compared to companies still using manual, paper-based processes.
Drive Operational Excellence With Food ERP
Dedicated food ERP software is the ideal starting point for your digital transformation as it offers features for various business functions and serves as a unified, organization-wide platform. An industry-specific ERP solution can help streamline your operations and promotes automation by integrating diverse business processes whether your company manufactures or distributes food and beverage products.
The software also fosters better collaboration and communication between departments, acting as a “single source of truth” for your entire company by providing accurate and consistent data. What’s more, an advanced ERP—like Aptean Food & Beverage ERP—can generate real-time metrics with integrated Business Intelligence (BI) features, enabling you to leverage the actionable insights they offer.
Deploying food manufacturing ERP software in your operation can unlock robust functionalities, including:
Recipe and Formulation Management — Configure your recipes and formulas with precision to promote consistency and customer satisfaction.
Bi-Directional Traceability — Maintain visibility at every stage of the supply chain and review granular data down to the item level.
Inventory Management — Keep close tabs on your inventory to maintain optimal levels and ensure production needs are met.
Data-Driven Demand Forecasting — Create reliable projections of demand based on historical sales data to better align supplies.
Quality Control — Promote consistent quality checks at various supply chain stages to meet the expectations of today’s demanding shoppers.
Customer Spotlight: Pizza Joe’s
Pizza Joe’s recently deployed Aptean Food & Beverage ERP via the cloud. Now, the Pennsylvania-based business can leverage a fully modernized ERP solution to move beyond the limitations of an outdated, generic ERP system that lacked essential capabilities. Plus, the solution gives the company high data accessibility and comprehensive inventory management features.
“I’ve heard from our team members that their work is so much easier than it used to be and that’s just great to hear. Sometimes change can be terrifying, but if you do it for the right reasons, there’s usually a good result.”
Improve Asset Performance With EAM
As another step in your digital transformation journey, EAM software helps companies like yours maintain capital equipment and other assets—giving you full visibility into machinery performance and helping to extend expected lifespan with proactive maintenance management. The real-time, advanced analytics the solution provides facilitate strategic decision-making, help keep downtime at a minimum and reduce the risk of sudden production stops.
A food and beverage EAM platform is a flexible and scalable maintenance management solution—boosting profitability by enhancing asset reliability while streamlining maintenance processes.
Food operations using enterprise asset management software will take advantage of the following:
Preventative Maintenance — Implement preventative maintenance programs to help extend the lifespan of equipment, reduce downtime and avoid costly breakdowns.
Effective Work Order Management — Centralize the work order process and automate steps to manage them effectively.
Asset Tracking — Monitor asset performance and maintenance histories to inform your strategy and maximize uptime.
Customer Spotlight: CoreFX
CoreFX embraced the future with Aptean EAM, ditching old spreadsheets and boosting machine performance. This switch not only reduced costs but also cut downtime. Plus, the easy-to-use system improves maintenance scheduling, giving staff the power to do more—especially during busy seasons, preventive maintenance tasks and compliance checks.
“Assigning projects to the staff is a lot easier. It's simple for me to get the technicians the jobs that they need to do and it's a lot easier for supervisors and quality techs to get an issue in front of me.”
Achieve Continuous Improvement With OEE
As a metric, OEE takes into account availability, performance and quality to calculate a critical performance metric, allowing you to understand the overall state of your production processes. As a system, OEE helps you glean insight into where improvements can be made—boosting productivity, reducing waste and ultimately elevating your manufacturing operations.
In food and beverage manufacturing, OEE software serves as the compass guiding plant, production and shop floor managers; the ideal approach for continuous improvement to drive impactful change with optimized programs and results analysis.
Organizations that implement OEE systems can enjoy the following features:
Real-Time Performance Tracking — Maintain full visibility into performance and pinpoint the causes of bottlenecks quickly.
Yield and Loss Monitoring — Leverage user-friendly tools that show real-time production status.
Labor, Changeover and Sanitation Tracking — Measure all aspects of production by having helpful data on work hours, cleaning durations and changeovers.
Customer Spotlight: Monogram Foods
Monogram Foods has gone paperless and is now enjoying a fully digital interface that helps the business streamline operations and reduce downtime by deploying Aptean Process Manufacturing OEE. The company has achieved enhanced accuracy by eliminating the risk of manual errors in logging figures and readings. Implementing this solution ensures precise data recording and provides full visibility into key metrics—empowering their teams with real-time updates on operational performance, allowing them to promptly assess how operations are running and the remarkable results they are achieving.
“All in all, we've had a significant uptick in overall equipment effectiveness at all of the plants where we've installed Aptean OEE. We've seen a rise of 10 points in OEE and those in the food industry running high-volume lines will recognize that's a big number.”
Kickstart Your Digital Transformation With Aptean’s Integrated Digital Ecosystem
Aptean’s food and beverage manufacturing software trifecta—ERP, EAM and OEE—is a gamechanger for our customers. Existing as an integrated digital ecosystem, our software solutions empower better resource management, greater asset reliability and increased operational efficiency and automation.
In addition, our team of experts possess collective decades of experience in the food and beverage industry so they’re aware of the real-world challenges you face and can provide invaluable best-practice advice. Our cloud-based solutions also offer advanced data security and operational agility with no expensive hardware purchases or additional data center expenses.
Learn more on how you can future-proof your manufacturing operations with this helpful guide: 7 Ingredients to Accelerate the Growth of Your Food and Beverage Company.
Alternatively, you can explore software options by taking our digital transformation quiz or have a quick chat with our experts today.
Prêt à transformer votre entreprise ?
Nous avons les solutions ERP spécialisées dont vous avez besoin pour relever les défis de votre secteur.
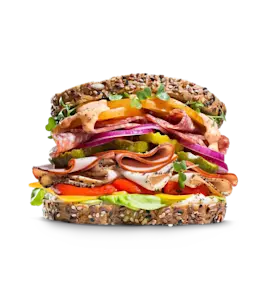