Featured in this post
4 Reasons Automating Manual Processes Is Essential for Discrete Manufacturers
4 Reasons Automating Manual Processes Is Essential for Discrete Manufacturers
Feb 14, 2023
Aptean Staff Writer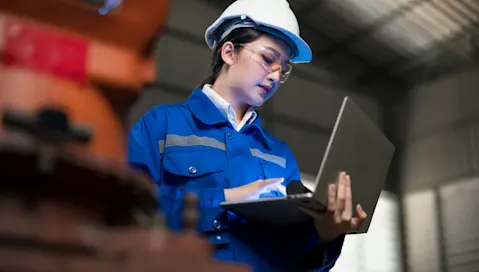
Are you tired of manually sifting through paperwork and inputting data? Feeling a bit like a hamster on a wheel?
It's high time to move forward with discrete manufacturing automation. A McKinsey study showed that the world can save 749 billion work hours by automating 64% of manufacturing tasks.
Many manufacturers have already made this shift. Aptean surveyed over 250 North American manufacturing companies for our 2023 Manufacturing Forecast, and found that 80% of manufacturers are already using technology and automation to drive their business's growth.
Have you considered an industry-specific enterprise resource planning (ERP) solution to help you leverage discrete manufacturing automation to its fullest effect? With a purpose-built industrial manufacturing ERP you can achieve automation and efficiencies across your business through tailored functionality.
Manual processes, like using spreadsheets to schedule operations and track inventory, can be a thing of the past. So if you're ready to make this a reality in your business, let's dive in and explore how automating discrete manufacturing processes can be achieved with an advanced industry-specific ERP.
1. Built-In Reporting and Analytics
Aptean’s 2023 Manufacturing Forecast shows that 38% of manufacturers have started gathering data automatically and using analytics to produce business insights compared to the previous year’s survey results which indicated only 23% of respondents had taken this critical step forward. This year’s findings are a testament to how discrete manufacturers value data analytics.
An ERP system provides an all-in-one solution that gives you a single source of truth through consolidation and standardization of data across your business. To further this, Aptean Industrial Manufacturing ERP can provide in-depth data analysis and reporting of key performance indicators (KPIs) through its Business Analytics feature.
This means you can leverage your ERP to turn financial and operational data into strategic insights, allowing you to focus on making data-driven decisions that improve your business instead of spending time aggregating all the data and compiling reports manually.
2. Improve Data Accuracy and Visibility
Accurately managing inventory data and having a streamlined production process are critical to discrete manufacturing success. Data accuracy and a single source of truth are two of the biggest benefits you can acquire using ERP software. Automating discrete manufacturing processes promises precision more than anything else, offering less room for human error. For instance, manual data input is prone to errors in transpositions, typos and other general mistakes that can lead to incorrect inventory levels or production schedules.
Aside from data accuracy, a specialized discrete manufacturing ERP system enhances data visibility and shows it all in real time. Manufacturers like you can easily use live data as a reference for your important business decisions, ensuring no opportunities are wasted. Automating manual tasks allows you to stay on top of the competition, allowing for more consolidated inventory management and tracking that can be accessed in real-time by everyone in your organization.
Aptean Industrial Manufacturing ERP has real-time operations data readily available within the same portal as employee data—all notes around a specific process or malfunction are visible to any party that needs to know. Having data accessible this way allows manufacturers to oversee all inventory and production-related figures and adjust accordingly; making operations streamlined and efficient.
of manufacturers are already using technology and automation to drive their business's growth
3. Superior Planning and Scheduling
The rise of e-commerce has disrupted the industry and changed how discrete manufacturers do business—from manufacturing to logistics. It has also given birth to unique business models like make-to-order (MTO) that allows customers to customize their products without any constraints.
An industry-specific ERP solution capable of handling planning and scheduling on the fly is necessary to match customer demand. It also allows you to cater to customers’ desire for freedom of choice when selecting what they can order while also balancing your supply with expected orders.
The MetalWorking Group (MWG) is a case in point of a manufacturing organization taking advantage of the scalability and scheduling options provided by a dedicated ERP solution. Aptean helped MWG reach promising growth in its metrics while solving issues regarding visibility and manual repetitive scheduling processes through the Advanced Scheduling module of our industrial manufacturing ERP. MWG was able to see an improvement in its shop floor visibility and efficiency and has improved on-time delivery from 75% to 86% in less than a year.
Not having a concrete schedule to cover weeks or even months of your production is a ticking time bomb. Not only will it hinder the amount and quality of the products, but it will also increase the waste that comes with it, either resources or actual materials.
With the right ERP solution from Aptean, you can calibrate all your planning and scheduling routines; manage jobs by seamlessly simplifying plan revisions due to components affected by any last-minute planning or scheduling modifications, identifying potential bottlenecks and decreasing down-time.
4. Cutting Operational Costs
Manual processes are time-consuming and introduce a level of human-error. Depending on where the error occurred and the magnitude, this can have a large negative impact on your operations. Every minute you spend trying to correct the problem is another minute of lost productivity and takes away from your bottom line.
A cost-effective strategy to prevent this is to implement a purpose-built industrial manufacturing ERP solution to help you run your operations more efficiently by automating discrete manufacturing processes. For instance, using automated billing and invoicing to streamline and save labor hours on the accounts receivable process. Or, using barcode scanners to remove the challenges that data entry brings.
And with Aptean Industrial Manufacturing ERP, you’ll benefit from the margin analyzer feature that tracks job costs and profits so you can compare the results against earlier estimates. This makes it easier to optimize and provide valuable cost insights for the team. You can also use the tool to calculate the profit margin for individual jobs and isolate all material, labor, production and subcontracting costs.
It’s no surprise that our recent study found that 89% of organizations say that technology will be a driving factor to help them increase their efficiency. On top of that, a third of the manufacturers have already taken the initiative and invested in software to help cope with the rising costs.
Choose the Right ERP and Remove Manual Processes Forever
Discrete manufacturing automation can be a process with many steps, but with the right approach and software partner, it can be a smooth and promising journey. The right ERP solution can help you optimize and improve your discrete manufacturing operations. In fact, our 2023 Manufacturing Forecast found that 98% of manufacturers have already outlined their digital transformation roadmap, realizing that fully embracing automation will be a critical path item to drive their productivity upwards and increase their profits.
So what are you waiting for?
Here at Aptean, we’ve helped countless discrete manufacturers kickstart their digital transformation journey with Aptean Industrial Manufacturing ERP. Our ERP utilizes modern and sophisticated scheduling algorithms and real-world capacity, material and time constraints to set delivery dates with real-time capability to promise. What’s more, our solution isn’t limited to traditional ERP functionalities, since we have implemented scheduling capabilities with supply chain management (SCM), customer relationship management (CRM) and business intelligence (BI) tools in one comprehensive package.
With Aptean’s Industrial Manufacturing ERP solution for your business, you can eliminate costly and inefficient manual processes and replace them with efficient, time- and labor-saving automations. If data entry, customer demands, planning and scheduling or heavy operational costs are taking a toll on your manual processes, it’s time to jumpstart your modernization and transform your operations with Aptean Industrial Manufacturing ERP.
Ready to learn more about Aptean Industrial Manufacturing ERP and how it powers efficiency-boosting automation? Contact us today or request a personalized demo.
Start transforming your business today
If you’re ready to take your discrete and industrial manufacturing business to the next level, we’d love to help.
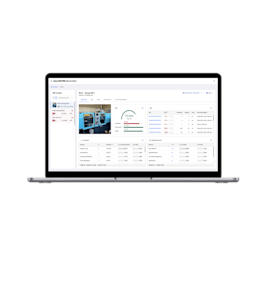