Big Data and You: Things to Consider Before Industry 4.0 Tech Adoption
Big Data and You: Things to Consider Before Industry 4.0 Tech Adoption
Big Data and You: Things to Consider Before Industry 4.0 Tech Adoption
Dec 6, 2018
Aptean Staff Writer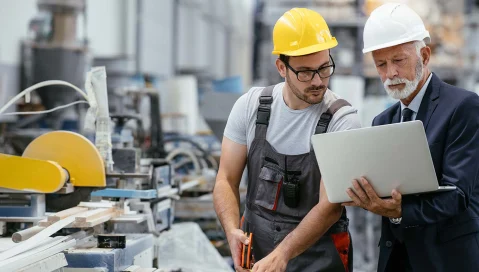
Throughout our Big Data & You series, we’ve discussed several benefits of adopting Industry 4.0 technology. Some of the benefits include greater visibility, increased efficiency and workflow and delivery predictability with improved tracking and reduced costs. These are all within your reach, but you don’t necessarily need advanced IoT technology to achieve them.
As you consider where you may need to upgrade your systems to meet Industry 4.0 demands, consider what you can achieve with the technology you have in place. Here’s some food for thought as you consider moving toward Industry 4.0.
What’s on Your Factory Floor?
It’s tempting to invest in the latest and greatest in warehouse technology – but that doesn’t mean it’s the right choice for your operation. In fact, some of the devices and solutions you’re already running could provide you with a better foundation for gaining efficiency than robots will.
Start by taking stock of every piece of equipment in your current tech ecosystem. For instance, consider your programmable logic controllers (PLC). PLCs control the flow of your processes, track production levels, and cut off operations based on a specified timeframe/production count to avoid waste or malfunction. But PLCs drive more than just day-to-day operations – they record data from your processes, giving you the visibility you need to make adjustments without investing in IoT-enabled sensors. You’ll find that many of the measurement devices and control networks you employ will also provide helpful data for designing smarter manufacturing processes.
Advanced technology can provide the data you seek for better decision-making, but before you invest, dive into the data already available within your systems and focus your efforts on filling in the gaps, rather than duplicating your existing collection efforts.
Are You Using Your Technology to the Best of Its Abilities?
You may find that your factory floor equipment is pulling more data than you realized – but now it’s time to consider how your current software solutions can assist in understanding your analytics so that your factory can shift to data-driven decision-making.
Perhaps the most important factor in maximizing your solutions’ capabilities is ensuring that they’re working in harmony. Legacy enterprise resource planning, warehouse management, enterprise asset management and other systems collected data, but because they functioned separately, they weren’t speaking to each other, so, for example, your factory floor and warehouse couldn’t see into each other’s operations. Today’s solutions, however, are designed to work together. By integrating your manufacturing systems, you’ll have better visibility into your data, as well as a simpler process for tracking improvements and making adjustments when necessary.
Understanding the benefits of the software and hardware you already maintain – and learning how best to leverage the data they produce – will make a significant impact on your processes before you spend a cent on IoT-enabled technology.
How Will Tomorrow’s Technology Improve Your Processes?
It’s important to remember that Industry 4.0 technologies don’t need to touch every area of operation. Set aside your processes that already work like a well-oiled machine, as re-investing in these areas may negatively impact productivity and drain resources. Instead, target your search to the technologies that address your pain points, and don’t let vendors sell you on solutions you don’t need.
If your inefficiencies run deep enough that you need to refresh your operations enterprise-wide, know that digital transformation does not have to happen all at one time. Think of adoption and implementation like moving into a new home. You get into this new, bare space with the urge to quickly fill it up with things that make you cozy. But doing so in one sweep might not be financially feasible, so you purchase items one at a time. Similarly, manufacturers should prioritize their pain points and identify where to start leveraging new technologies while developing a plan for continued expansion.
Keep Moving Forward – but Don’t Forget to Look Back
It’s true that shifting to Industry 4.0 technologies is a lengthy process, but if you select the right partner for the journey, there’s no reason to be intimidated. The purpose of Industry 4.0 is to empower. Before launching a digital transformation initiative, take a breath and evaluate your options to ensure that you’re making an informed decision. Capitalize on the technology you already have in place, while setting a steady pace for how your company will leverage new technologies to achieve the improvements you seek.
Interested in reading the rest of our Big Data & You series?
Start transforming your business today
If you’re ready to take your discrete and industrial manufacturing business to the next level, we’d love to help.
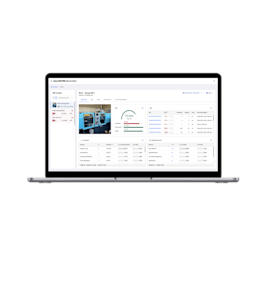