Featured in this post
11 ERP Implementation Best Practices
11 ERP Implementation Best Practices
Aug 5, 2021
Aptean Staff Writer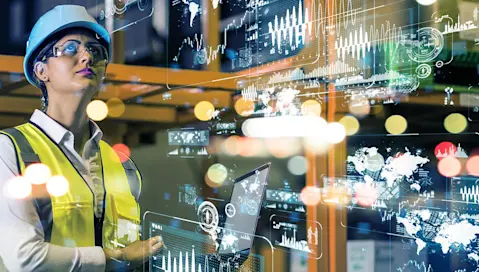
When you decide to incorporate an enterprise resource planning (ERP) solution into the folds of your enterprise, it's a really big deal.
It's going to transform the way you operate. And, undoubtedly, it'll affect every single person on your team.
Change is a good thing. It means progress and growth. But change can also be really hard.
It's our goal to make this transition and ERP implementation as easy as possible. So we talked to a handful of our current customers—those who went from disparate systems that don't integrate well or who were implementing an ERP system for the first time or were looking to replace an existing system that no longer met their needs.
And we asked them about their implementation process: what went well, what didn't, what they wished they knew. And their responses were really enlightening. Don't just take our word for it. Read for yourself.
Here are the 11 best practices from people who have actually experienced an ERP implementation.
1. Recognize Your Business's Needs and Goals
Before implementing a new ERP solution, it's essential to consider your business's actual needs. What are you hoping to gain from implementation? What problems are you hoping to solve? What requirements will each function need? An ERP is not a simple fix to a small problem. It's not just another workaround. It's the foundation of how you operate, of how you choose to move your business forward.
Our customers recommend working across your entire business to develop documentation of comprehensive business requirements and needs. This will ensure the ERP you select will deliver what you're expecting.
Along those same lines, you must know what your goals are before beginning implementation. You can't get what you want unless you know what you want.
Eric Vosburgh, a Senior Business System Analyst at Tasus Corporation, says that it's essential that you "understand what does not work for you currently [and to understand] what your goals are" as you move forward with implementation.
2. Recognize the True Functionality of an ERP Solution
Dolores Lancaster, a Financial Cost Analyst at Branding Iron Holdings, Inc., says, "A clear understanding of the fully-integrated nature of an ERP system is PARAMOUNT! Otherwise, garbage in becomes garbage out. What every employee keys into the system impacts the entire system!"
To know the full power and potential of an ERP system is crucial to being able to use it to its full functionality. There's so much that ERP software can do for you and your business—but to utilize it, you must first put in the time to explore and understand it.
It's also a good idea to map the functionality of ERPs you're considering back to the needs and requirements of your business. By conducting this internal mapping exercise, you can guarantee you're getting the functionality and capabilities you're looking for.
3. Select the Right ERP Partner
When it comes to the right ERP partner, Jai Balasubramanian, a business analyst at Creative Co-Op, Inc., says, "The stability of the ERP vendor and the quality of their support" is invaluable to implementation success.
Selecting a partner who knows your industry, who has that expertise and industry-specific knowledge, will make the transition process that much easier. They should be able to share and provide best practices they've learned from other implementations within your industry.
4. Track Your Data Before, Throughout and After ERP Implementation
Dolores Lancaster recommends the importance of data integrity throughout the entire ERP implementation process. So take care of it, and track your data at every stage of the process. Lancaster urges you to ask yourself, "What processes and policies are going to be put in place to ensure the integrity of the data being entered into the system?" And then, after all that data is in the system, it's essential to track it.
Lancaster adds, "A plan to systematically archive no longer relevant historical data should be included in the ERP plan, so to responsibly manage your data and storage and have the ability to retrieve data in a timely manner."
5. Consider How This ERP Implementation Affects Your Current Processes
It's important to understand that many of your current processes will need to change and/or adjust to this new way of doing things with an ERP implementation.
Craig Cormier, an IT Manager at Anderson Power Products, would encourage anyone considering ERP implementation to think through the following questions, "Is your business ready to commit itself to the work needed? Is it willing to adapt its culture and processes to new ways, or will it struggle to adapt the system to match their old ways?"
If you expect success in your ERP implementation, you must be willing to reform all your current processes—even the ones that work well. It's a lot of work at the beginning. But in the end, it'll be so much easier for you and your employees. All your data and processes are centralized within a single source of truth.
Eric Vosburgh, Senior Business System Analyst at Tasus Corporation, thinks it's essential to question how the software interfaces: "Will there need to be changes and how do those affect the users? Get the users involved in this process. They are your best resource of information." To really ensure that your processes work, involve team members throughout implementation—don't wait until it's over. Otherwise, processes may be incorrect and the wrong teams may be affected, which could lead to a low adoption rate.
Tim Ringle, a developer at Gehl Foods LLC, advises, "Be sure to minimize the amount of process change that occurs during an upgrade. This will minimize risk."
6. Generate a Realistic Timeline
Implementing an ERP solution is not going to be a quick, overnight success. It would be best if you recognized this at the beginning of the process.
Manage your expectations and know that there will be a learning curve for you and your employees, just like with anything new. Many of our customers recommend a phased approach to implementation. This will ensure you're not trying to rush through the process and allow enough time to implement each module effectively and adequately.
It takes many resources and commitment to implement a new ERP system, so a phased approach can help alleviate some of this pressure.
7. Include Testing and Training in Your Timeline Projections
It's so important to be patient throughout the process. You will need to test the system again and again. And when you think you're done, test again. It's an ongoing process.
Working toward a thoroughly tested system is more important than meeting a deadline that doesn't allow comprehensive testing.
Howard Hawkins, an IT Manager at Cardinal Scale Manufacturing Co., advises anyone beginning the ERP implementation process to take their time, document their processes, and "follow the flow through the processes and steps needed to get the desired result. Test your documentation periodically by giving the instructions to someone that isn't the main person doing the process and see if it can be accomplished. This will give you a backup in the case of employee turnover."
Repeatedly testing the system minimizes issues and creates a smoother go-live for end-users.
It's also valuable to in include ample time for training and adoption of the system in your ERP implementation schedule. Dolores Lancaster, Financial Cost Analyst at Branding Iron Holdings, Inc., says it's essential to take your time: "A clear training program where employees have hands-on experience and time to 'play' in the system prior to go-live, so that the transition from the current system to the new system is smoother and much less of a culture-shock."
Lynn Limberg, ERP Specialist at Climate by Design International, Inc., elaborates on this point; implementation is not something to be rushed. She says it's critical that you "install [a] test system and thoroughly test your data. Take your time [and] train on the system and processes." Take your time to test thoroughly—it'll be worth it in the long run.
8. Ensure Your Executive Team is on the Same Page When It Comes to ERP Implementation
"The most important thing to guarantee the success of an implementation is executive support for the implementation. For maximum effectiveness, the entire organization must document and exercise the processes in the system to ensure minimal impact on customers. This is going to reduce the organizational bandwidth for other changes that may be desired by the business," stresses Tim Ringle, a developer at Gehl Foods LLC.
The importance of obtaining executive buy-in, commitment and adoption from the top down is essential. If leadership sets the example that this implementation is a good, positive change for the businesses, the employees will adopt that same mentality.
9. Include Your Entire Team in the ERP Implementation Process
It's not only essential to get your executives involved, you also need to ensure key team members and stakeholders are involved in the entire process as well. Our customers believe it's invaluable to include the entire team in the implementation process. Anybody using the system, not only the executives and decision-makers, should be involved in the process itself.
Jeff Carroll, the IT Manager at Sudenga Industries, says, "Company acceptance from top management to the shop floor is key." Teamwork is instrumental in successful ERP implementation, and it's hard to know which questions are important to ask. Carroll suggests involving leadership from sales, production, accounting, wherever you think is valuable in the process, so they can consider and question how the new software will affect their respective departments.
After all, as Carroll says, "ERP [software] is a way of handling the inner-workings of your business, [so you must] make sure all involved know this. It takes teamwork and perseverance."
Dolores Lancaster, Financial Cost Analyst at Branding Iron Holdings, Inc., shares Carroll's sentiment: "Every employee needs to have an understanding of what module and department feeds their module and how what they enter into the system delivers and informs the next employee/department to do their job."
Additionally, Lancaster is an adamant believer that "every department should have a champion that understands the module(s) that their team primarily works in and how the ERP system will help them work smarter (not harder)."
10. Consider Whether or Not You're Really Ready to Go All-In
This kind of system only works when your organization is genuinely committed to making it work. So if you're implementing with any reluctance, or attempting to bend the ERP system to fit the shape of your old processes instead of the other way around, then the implementation will never work.
You must be willing to adjust your company culture, your company processes and your company methodology. As we said initially, change is hard, but change becomes even harder when you're unwilling to commit fully to the major and minor adjustments alike.
IT Manager at Cardinal Scale Manufacturing Co., Howard Hawkins, advises that you make sure everyone is on board, "Is there a commitment? You can have the best software, but if there is not a commitment to 'make it work,' you won't have any better result than using whatever you are doing now. Not only management buy-in but employee involvement."
11. Ensure the System is Preparing You for Now and for the Future
Ryan Fonash, the Director of Information Systems at Vintage Imports, Inc., says that you need to look at this implementation from all angles: "This is the software that will run your company for the foreseeable future. You want to ensure that you are flexible with your business practices and/or that the software is flexible because it won't necessarily match what you are currently doing. Try to think about where you envision your company in 10, 15 years and the kinds of things you'd like to be doing.
Can the software grow with you? Is the software vendor constantly innovating and building out new capabilities? How often are they releasing new versions, and what is your upgrade path - is it something that is truly feasible? Or are you going to be stuck on an old version due to various constraints?"
These are the essential questions to ask when it comes to the success and stability of your business for years to come. ERP implementation isn't an overnight fix. It's not a band-aid. It's a solution that grows and matures as your business does. You now have some of the tools you need for a successful ERP implementation.
Aptean ERPs are built with you in mind.
We've created an out-of-the-box solution to fit the needs and demands of your industry. We have the right ERP for you, whether on-prem or in the cloud—from food and beverage to electronics to consumer goods to anything in between.
If you're still trying to figure out which ERP or vendor is right for you, take a look at our list of the top 10 ERP selection criteria. Or, if you're ready to learn more about Aptean ERPs, contact our expert team today.
Get in touch with one of our ERP software experts today
To accelerate growing your business, you need an ERP solution built specifically for your industry. We're ready to help—reach out today to request a callback.
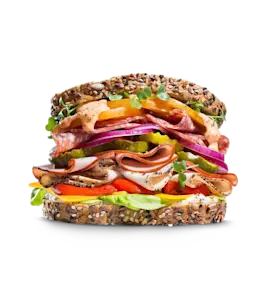