Using Real-Time Data to Keep Up with Surges in Food Demand
Using Real-Time Data to Keep Up with Surges in Food Demand
Using Real-Time Data to Keep Up with Surges in Food Demand
29 Juli 2020
Joey Carabetta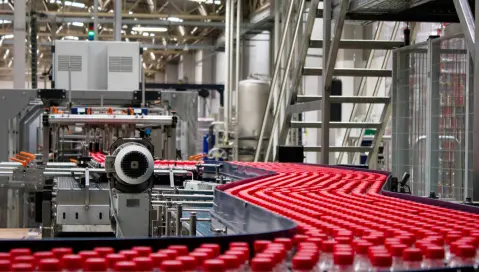
As the U.S. continues to grapple with the deadly coronavirus, the food manufacturing industry is feeling the effects of shelter-in-place restrictions, restaurant closures and a battered economy.
An article published July 12 in The Wall Street Journal highlights how a number of the country’s largest food manufacturers — including General Mills Inc., Campbell Soup Co. and Conagra Brands Inc. — are struggling to keep up with supply, even as they continue to pump out food as fast as they can.
Popular grocery items such as flour, canned soup, pasta and rice remain in short supply across the U.S. as Americans eat more at home and safety measures at manufacturing plants slow operations.
“We are running flat out,” Conagra’s Chief Executive Sean Connolly tells the WSJ of building up inventory of certain brands, including Chef Boyardee and Healthy Choice.
To get to normal levels of inventory again, Connolly said demand must slow or further increases in manufacturing capacity will need to be put in place.
Campbell’s Soup CEO Mark Clouse tells the WSJ that the surge in demand for pantry items has created a shock to its supply chain, which was dealing with flat or falling demand prior to the pandemic.
“We’re racing to try to rebuild some inventory,” Clouse said.
To deal with unexpected surges in demand, manufacturing companies look to business software like manufacturing execution systems (MES) to help improve production output, identify manufacturing losses in real time and gain visibility into overall plant performance.
Below, we outline how an MES gives food manufacturers the end-to-end visibility and access to real-time data they need to keep up with surges in demand and ensure success.
Increasing Capacity
To keep up with pandemic-related demand, food manufacturers need to increase production – it’s as simple and as complex as that. Increasing manufacturing capacity means producing more product to keep up with new demand. But it also means examining existing workflows, identifying losses, cutting down on waste, reducing downtime and reassessing a number of other critical factors that all play a role in a business’ manufacturing processes. In short, increasing productivity as demand surges is complicated.
An MES uses real-time shop-floor data to give operators, supervisors and executives actionable intelligence and complete visibility into production. It provides full manufacturing visibility from batching through to packaging to deliver real-time metrics that enable companies to run simpler, smarter and more strategically.
The number one question we at Aptean hear from executives is: “How do I increase capacity with the plant I already have?”
Our answer is almost always the same: “With access to immediate, actionable intelligence.”
Most food manufacturers who struggle with production capacity don’t have insight into their problem areas or aren’t even aware that problem areas in their plants exist. Without this insight into your operations, it’s impossible to make production decisions or changes that will increase productivity.
Companies who are unable to accurately measure and track sanitation times, for example, risk losing valuable production time if sanitation processes take longer than expected. A solution like an MES will track sanitation timelines, giving you the ability to drill down into the data and make small adjustments that will minimize the impact on run time.
Reducing Giveaway
Increasing production output without truly understanding yield loss can result in product over-packing, material shortages and lost money. To keep up with surging demand, manufacturers must accurately measure giveaway to ensure they are hitting production targets.
Here’s an example: Your staff in the packaging department is filling containers with 17.2 ounces of product instead of the required 16 ounces. There’s no system in place to flag this discrepancy and no one on the packaging line is manually noting these inconsistencies when they perform their sample checks. As a result, your plant runs out of product to fill the rest of the day’s orders and you miss fulfillment targets. It takes you until the following morning’s production meeting to realize that you’ve given away thousands of pounds and dollars of product.
An MES is linked to a plant’s quality processes, scales and production lines, so variances in quantities or measurements are flagged in real-time and operators are notified of issues immediately. In the example above, an MES would alert operators that the filling machines need to be recalibrated, decreasing your giveaway and increasing the amount of product you’re able to ship out.
Improving On-Time, In-Full Performance
Maintaining On-Time, In-Full (OTIF) numbers under normal circumstances is tough. Add in a pandemic and constant supply chain disruptions, and meeting OTIF requirements can seem impossible.
An MES provides real-time visibility into how an order is progressing through the production line and measures if it’s meeting planning targets to be completed on time. With this insight, manufacturers can better plan labor deployment, schedule sanitation and changeover times accordingly, and work to drive productivity improvements to ensure every order is completed accurately and on time.
Food manufacturers who struggle to hit OTIF requirements also struggle with a lack of communication between operators, supervisors and executives. With an MES, production plans and schedules are readily accessible, so everyone in the plant is aware of the plan along the way. Collaboration tools built into a solution like Aptean Factory MES help centralize various forms of communication from across your organization into a centralized platform. This open collaboration system gives everyone on the shop floor a voice to track and resolve issues in real time.
To keep up with surges in demand, food manufacturers must find a way to improve operational efficiency. Aptean Factory MES helps food companies increase production capacity, reduce giveaway and meet OTIF requirements. If you’d like to learn more about how this powerful solution can help your business ensure success in these uncertain times, reach out to us. We’d love to talk.
Sind Sie bereit, Ihr Unternehmen grundlegend zu verändern?
Wir bieten Ihnen die spezialisierten ERP-Lösungen, die Sie für die Herausforderungen Ihrer Branche benötigen.
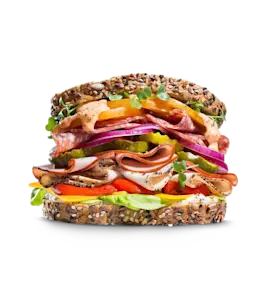