Food Manufacturers Are Going Paperless: Automate Quality Tracking With OEE Software
Food Manufacturers Are Going Paperless: Automate Quality Tracking With OEE Software
Food Manufacturers Are Going Paperless: Automate Quality Tracking With OEE Software
Sep 19, 2023
Aptean Staff Writer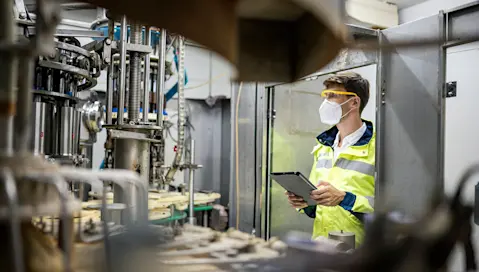
To meet the demands of today’s competitive landscape, the majority of food and beverage manufacturers have already invested in digital transformation initiatives and gone paperless in their operations—replacing their paper-based system by digitally transforming customer support, procurement, inventory control, manufacturing processes and accounting.
Switching to a digital strategy offers your business a competitive edge by ensuring product quality while optimizing operations—allowing you to bring products to market faster, minimize supply chain complexities and improve connectivity throughout all facilities. Based on the IDC whitepaper, Global Food and Beverage Industry Trends and Strategic Insights 2022, up to 55% of food and beverage companies expected to see even greater improvements across their production, quality, supply chain, logistics, sales and more with their digital journey.
Indeed, paper-based systems have significant disadvantages that may hinder accessibility and jeopardize the security of your data. Manual methods also limit collaboration and communication within your workforce and are prone to inevitable human error, making it hard to monitor equipment effectiveness and quickly address operational disruptions.
Overall equipment effectiveness (OEE) software provides real-time monitoring of your capital equipment's performance while giving insights into its effectiveness and reliability. In this blog, we’ll provide an overview of OEE as well as its features and advantages of tracking productivity, asset availability and quality to optimize plan attainment in your food manufacturing operations.
What Is OEE?
Overall equipment effectiveness uses production metrics to assess and improve manufacturing performance. It can help promote continuous improvement (CI), increase production volume, reduce wastage and scrap, and improve shop floor visibility and accountability.
The equation includes the following production metrics:
OEE Score = Availability x Performance x Quality
The OEE score is calculated by multiplying your operations' availability, performance and quality (APQ) variables. While a score of 100% is the perfect scenario in a production run, it’s difficult to achieve; a score of 85-98% for OEE is a good standard to aim for.
Hence, a good OEE platform must provide real-time insights and data-driven reports to help you boost your capital equipment's availability, performance and output quality.
Why Go Paperless on Your Production Floor?
Going paperless is an effective method to maximize efficiency in your production and quality processes—replacing physical documents with automation and digital techniques helps reduce costs and increase productivity. It involves deploying software solutions, such as an OEE, to manage all the data collected for your manufacturing operations, helping to reduce inevitable human errors and inaccuracies from manual recording.
By implementing digital strategies, you can automate data collection with sensors on your production line that capture real-time data and integrate it into the OEE platform. With the solution's collaborative dashboards, your team has instant visibility into messages, tasks, notes and up-to-date production data. Going paperless saves time and promotes high production accuracy.
Indeed, implementing digital systems promotes a "paperless culture" in your organization as these digital transformations can help seamlessly transition from tedious paper-based processes to more convenient (and more accurate) digital methods.
Advantages of Adopting Paperless Quality and Production Processes With OEE
Moving to a digital, automated method can modernize your manufacturing business and future-proof your entire process. You can boost plan attainment with capabilities like labor planning and tracking for work shifts and production lines, yield tracking and sanitation/change-over and clean-in-place (CIP) process automation.
In the food and beverage industry, the transition of going paperless provides benefits beyond cost and time savings which include improving operations and maximizing resources.
Beyond the surface benefits of shifting to digital files to free up office and shop floor spaces while eliminating paper waste, when it comes to data security, digital documents housed by online platforms are well-secured and more convenient for your staff and customers.
Let’s now look at some of the operational business advantages of going paperless.
1. Streamlined Data Collection and Recordkeeping
In a study, U.S. employees spend around four weeks every year looking for lost documents in their paper stacks. Software solutions allow easy access to files and other information anywhere through a centralized database.
Holding the most substantial value in businesses today, your data can affect your operations, strategies and business outcomes. Data collection is the foundation for identifying inefficiencies, slow runs and continuous improvement opportunities. OEE systems simplify this data collection and analysis by allowing you to capture information within a single source of truth using sensors on your production lines.
This approach to recordkeeping reduces time spent on manual data entry while minimizing errors and boosting the quality of the data from the frontline. OEE systems can also be integrated with enterprise resource planning (ERP) systems for data synchronization to further streamline processes.
2. Efficient Data Accessibility and Analysis for Continuous Improvement
Data analytics provides insights into your processes and product quality and can help you identify areas for continuous improvement while making data-driven manufacturing decisions quickly.
OEE systems also help to identify the processes that need improvement by collecting accurate, real-time data allowing your operations to adjust quickly to any manufacturing issues.
3. Optimized Quality Control Processes
Quality control's primary objective in manufacturing is to provide top-notch products to your customers. Moreover, quality control processes create a holistic approach to enhance all parts of your business including risk management, compliance and product innovation. OEE systems can help you optimize your quality control by promoting the aforementioned continuous improvement to meet consumer demands.
Food and beverage manufacturers can manage real-time product quality checks. Our Quality Module provides vital pass/fail metrics with rapid supervisory sign-off and generates automated quality assurance results. The module has a direct link to bar-coding and image-recognition hardware to adhere to compliance.
4. Efficient Collaboration and Communication Through Cloud-Based Systems
While eliminating physical paper archives from your shop floors, OEE solutions help ensure all your files are secured with increased data protection. Moreover, cloud-based OEE software allows your workforce to access data anywhere, promoting streamlined communication among your team members.
The digital collaboration dashboard provides full visibility of the shop floor and other areas for your operations; an ideal tool to track and resolve issues in the production line through automated notification messages, tasks and notes.
5. Ensuring Compliance and Regulatory Standards
When going paperless with proper digital systems like OEE, you can have visibility into every aspect of your manufacturing process helping to ensure compliance to regulatory standards by allowing you to create digital signatures and utilize digital forms, tracking systems and other statutory requirements.
Aptean Process Manufacturing OEE's Quality Module has a full suite of SPC tools to track and manage compliance that's aligned to initiatives such as:
Successful Companies That Implemented an OEE System for Automation
Here are some examples of manufacturers that have successfully leveraged Aptean’s Process Manufacturing OEE solution as part of their digital advancement.
Monogram Foods
Before Monogram Foods deployed Aptean’s OEE system, its inspectors reviewed a stack of paperwork whenever they needed data on their production and capital equipment. Often, spending time and resources browsing insignificant documents.
After deploying Aptean Process Manufacturing OEE, they are able to leverage a fully-digital interface that serves as a single source of truth across the organization. The OEE system has streamlined manufacturing operations by reducing downtime while also promoting consistently high-quality products. Monogram Foods also increased its OEE score by 10 points while maintaining high-volume production lines.
Aurora Organic Dairy
As one of the leading companies that supplies organic dairy products for many large-scale grocery chains, Aurora Organic Dairy needed to be more effective in tracking and analyzing downtime data. Operating without an OEE system, its Resin Loss team was losing $25,000 a month due to lack of visibility and the proper software to track the root cause of the loss. Hence, the company searched for a single system to promote efficiency, create quality control checks and track operational downtime.
After implementing the ideal OEE solution, Aptean Process Manufacturing OEE, Aurora Organic Dairy saved $200,000 in 8 months. Business leaders have since decided to replicate this initial success by expanding their OEE software to leverage its full capabilities.
Embracing Digital Transformation With Aptean Process Manufacturing OEE
Going paperless, the future of food manufacturing, is here now. By replacing labor-intensive paperwork, clipboards and whiteboards with up-to-date data analysis from OEE, food manufacturers can easily spot the reason for slow runs and machine breakdowns, reducing the overall impact of these unforeseen incidents.
All roads lead to digital shop floors with cloud-based solutions and real-time monitoring. An industry-specific and purpose-built software solution ensures that embracing digital transformation to optimize your paper-based processes will run as planned.
A reliable system like Aptean Process Manufacturing OEE can help streamline your data collection and recordkeeping, increase continuous improvement, maximize your quality control processes, and promote collaboration and communication while helping you to comply with industry regulatory standards.
Are you ready to jumpstart your digital transformation journey by going paperless with OEE? Have a quick chat with our experts today or request a personalized demo anytime to see solutions from our product suite in action.
Ready to start transforming your business?
We’ve got the specialized OEE solutions you need to conquer your industry challenges.
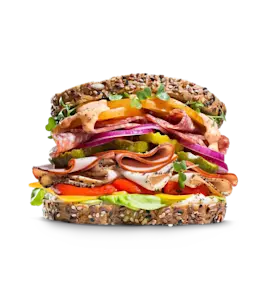