Factory MES: Keep Up with Evolving Regulations & Quality Compliances
Factory MES: Keep Up with Evolving Regulations & Quality Compliances
Factory MES: Keep Up with Evolving Regulations & Quality Compliances
Feb 11, 2020
Don Reese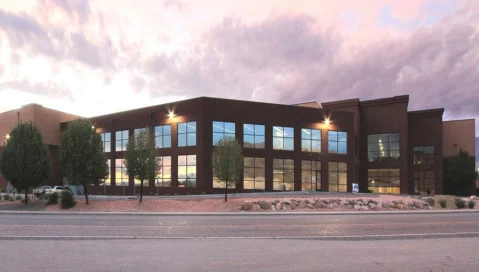
When it comes to running a factory, sometimes the long list of daily to-dos overwhelms the long-term needs of your organization. You figure you’ll just get to it when you get to it, but for now, it’s okay to put on the backburner for another day.
A manufacturing execution system (MES) is a solution that can help you stay ahead of the curve and be a part of the solution, particularly when it comes to meeting your food and beverage regulations and quality compliances.
This was especially true for Litehouse Foods.
I can speak to this personally. I’m Don Reese, and I’m a cost analyst at Litehouse. Aptean was a game-changer for us.
Every day, our factory produces a ton of data. Some of it we were using, some of it we weren’t, and some of it we didn’t even realize we were tracking or had the ability to track. The data we did have, however, was excellent. The only problem was… what to do with it. It can be a real challenge to accurately track, maintain, and keep up with the data.
Here at Litehouse, prior to Factory MES, all quality data was collected via paper checks. Each job had six to eight sheets of checks, and all checks were to be performed at set time intervals whether uptime or not. After production runs, checksheets were boxed up and taken off-site for storage.
In this process, concerns about quality check data integrity were common. Due to the manual system - tracking, reporting and identifying information was extremely challenging. Lack of real-time visibility and accuracy in reporting did not allow us to make the most accurate improvements.
With an increased focus on organic, non-GMO and Safe Quality Food (SQF) Certification, a paper-based system was not going to cut it anymore. We needed to get ahead of this, so we could make improvements to drive our growth and meet consumer demands.
Through the Factory MES quality management capabilities, we have been able to automate the calculation for each weight cycle, as well as run averages for the whole run. With this process, we have been able to design and implement accurate control limits for our products, which has allowed us to reduce yield loss through overfill tighter controls and preventative maintenance.
Additionally, with Factory MES being structured in a way that gives each individual production employee a unique digital username (signature) and password, we’re able to easily meet SQF compliance with electronic checksheets.
Real-time data collection of our quality information within Factory MES allows the QA teams to be ahead of the curve. Job level quality check information is now reviewed and signed off in a timely manner.
Historically, when customers contacted us with questions, concerns, or requests for additional information, the response time was challenging as paper checks had to be gathered, sorted and then a manual report compiled. With Factory MES we are able to pull data in real-time, consistently and in an easy to understand format, which reduced our response time by 80%.
By leveraging Factory MES, Litehouse has been able to properly comply with all regulatory requirements, improve quality consistency and gain access to real-time quality compliance data and information.
To learn more about the partnership between Litehouse and Aptean, read our full case study here.
Get in touch today to speak with an expert in your industry
To grow your business, you need a food ERP built specifically for your industry challenges. We're ready to help—reach out today and we'll help you find the right solution.
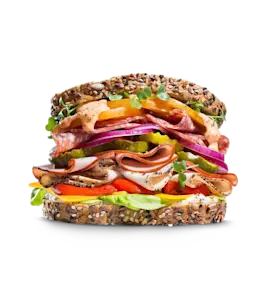