3 Compelling Reasons for Quality Management in the Food Industry
3 Compelling Reasons for Quality Management in the Food Industry
3 Compelling Reasons for Quality Management in the Food Industry
9 Jun 2022
Jack Payne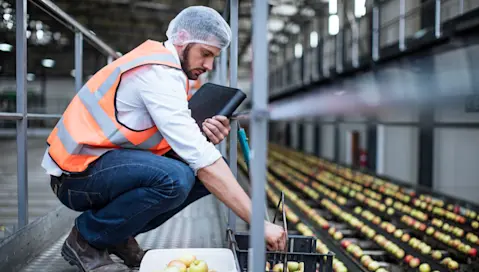
Many professionals in the food and beverage industry regard quality management as a “given.” It’s in your business’s best interest for your products to meet certain standards—those of government agencies and today’s consumers, namely—so it follows that you should build in checks to properly assess the key attributes of your items.
While this reasoning leads to the right conclusion, it oversimplifies what is in fact a complex and increasingly important topic. There are additional areas of concern that necessitate uncompromising quality assurance in all food and beverage processing, manufacturing and distribution scenarios, and regardless of how stringent your current procedures are, it’s worth revisiting the topic to understand it at a more holistic level.
Here, we’ll run down three of the primary reasons that food quality management matters and then close with a brief explanation of how an industry-specific enterprise resource planning (ERP) solution helps ensure you can make repeatable, reliable and scientifically based assessments of your finished goods.
1. Ensuring Food Safety and Compliance
The increased scrutiny on public health and the policies and practices that affect it may have been more prominent matters of discourse with the COVID-19 pandemic, but the truth is that this has been an important topic for decades. Food safety is a significant part of the equation, and for good reason—spoiled products, contaminated materials and undeclared allergens all pose considerable risks to consumers’ well-being.
There’s also the matter of maintaining full compliance, and governments around the world are rolling out more stringent requirements than ever before, including the U.S. Food and Drug Administration’s Proposed Rule on Traceability and the Food Standards Agency’s five-year plan that addresses our changing food systems. The potential costs of failure to adhere to these standards include fines, penalties and even business closure.
Together, these considerations make it clear that food safety and quality management must be approached proactively by defining your procedures, building in alerts or reminders to make sure they’re always carried out and prompting swift intervention in the case of a deviation from acceptable results.
2. Protecting and Bolstering Brand Reputation
Brand reputation, while intangible, is nonetheless invaluable for your business’s future. And more than your company history, logo or any marketing slogan, the perceived quality of your products in the eyes of the public is what determines how well-regarded you are in a market with increasingly high expectations.
Your teams have no doubt worked hard to build this aspect of your business, and implementing stringent quality management procedures is necessary in order to protect this investment of time and effort. By consistently enforcing high standards for every item that leaves your facilities and heads downstream to clients, you can establish trust and become the name to rely on in the sector you serve.
Consider also the potential of a major quality failure like a product recall. Besides the average monetary cost of $10 million, you’re likely to suffer a loss in future sales—a Harris Interactive survey found that 15% of consumers would never buy a product that had previously been recalled, and 21% said they’d never purchase from the associated manufacturer again in the future.
3. Maintaining Excellent Customer Satisfaction
You likely know from personal experience how disappointing it is to purchase one of your favorite products and open up the package in anticipation only to find that it’s defective in some way. It could be taste, texture, freshness or any of a number of other important characteristics that is intrinsically tied to quality.
Such situations can turn shoppers who might otherwise champion your organization’s goods and spread positive word of mouth into detractors or even outspoken critics. They also lead to less repeat purchases going forward, as there’s a loss of trust and loyalty that occurs when a food and beverage business lets down its faithful consumers.
Comprehensive and exacting quality management procedures are the best way to prevent subpar items from ever making it onto store shelves, which helps keep your biggest fans happy with consistently excellent items. Just remember, once you create those expectations, meeting them each and every time becomes even more important, which emphasizes the importance of never missing critical checks.
How ERP Technology Powers Better Quality Management in the Food Industry
We’ve pointed out several times how vital it is that your quality assurance practices are performed with each and every finished good, which means making them repeatable and reliable is a must if you want to be effective in your efforts. We’ve also stressed that your checks should be thorough, which makes an objective, scientifically based approach the best.
How do you check all those boxes and limit the chances that human error will result in a slip-up?
Purpose-built technology—such as our own industry-specific food and beverage solution, Aptean Food & Beverage ERP—is the answer. These powerful systems create a basis for digital transformation, acting as the bedrock and “single source of truth” for everyone in your organization.
With robust features dedicated to quality control, our solution is a cut above the competition, integrating with your equipment to import quality results in real time. It also helps streamline and automate the process, employing on-screen alerts to ensure that each procedure is followed precisely every time.
What’s more, our platform fosters collaboration between your departments as a cross-functional database, making important facts and figures highly visible for everyone from the shop floor up to the C-suite. Finally, there’s the additional advantage of our industry-specific technologies built on an underlying Microsoft Dynamics 365 Business Central framework and the option for a flexible, secure cloud-based deployment on a software as a service (SaaS) model.
Now, are you ready to learn more about Aptean Food & Beverage ERP and how it can help your organization effectively manage quality? Feel free to reach out to us today, or schedule a personalized demo to see the system for yourself.
Domina tu gestión integral de la calidad de los alimentos
Si estás listo para llevar tu negocio de alimentos o bebidas al siguiente nivel, nos encantaría ayudarte.
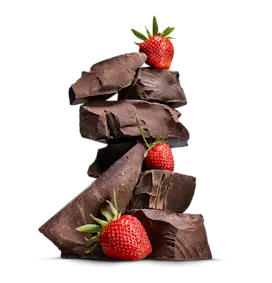