Destacado en este post
The 4 Reasons Traceability in Food Manufacturing Is Essential for Success
The 4 Reasons Traceability in Food Manufacturing Is Essential for Success
4 Ago 2025
Jack PayneEntrada en el blog
Want the Highlights? Here Are the Key Takeaways
This blog discusses the four most significant reasons that food traceability is crucial for businesses:
Complying with government regulations – Understand what’s required by law and avoid severe penalties.
Ensuring food safety and recall readiness – Protect the public health, as well as your brand reputation, and be prepared in case of a food safety emergency.
Providing full product transparency – Give consumers a clear picture of what they’re buying and build trust with the shopping public.
Avoiding food fraud – Protect your company from an increasingly common crime that can have serious negative impacts.
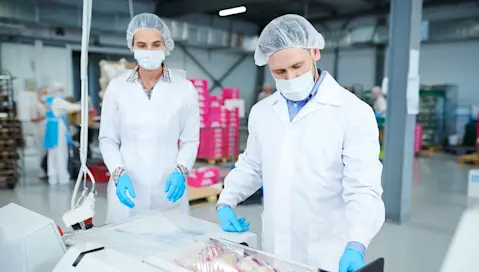
According to a recent research report published by Foods Connected, three in every four food businesses acknowledge the critical importance of traceability. There’s certainly plenty of money spent each year by companies to maintain supply chain visibility and bidirectional product tracking—the global food traceability market size is projected to grow beyond $35 billion USD by 2032.
That being said, even if you know how critical it is to have good food traceability procedures in place at your facilities, the reasons behind them may not be quite as salient in your mind. That makes now a good time to step back, remind yourself why food traceability must be a daily priority and confirm that your systems and processes are optimized to achieve success in this function.
In this blog, we’ll cover the four most compelling reasons behind the need for traceability in food manufacturing. We’ll also touch on how enterprise resource planning (ERP) can enhance your company’s effectiveness on this front and why now is the time to either jumpstart your digital transformation if you haven’t put a solution in place or re-evaluate your approach to traceability if you have already deployed a platform.
1. Complying With Government Regulations
The first steps toward codifying proper traceability practices in the food and beverage industry were taken with the creation of the Global Food Safety Initiative (GSFI) in 2000. Together with GS1, the organization established the Global Traceability Standard (GTS) to provide key insights and knowledge for organizations and industries developing long-term traceability goals.
In the following years, government agencies around the world have enacted legislation to further specify traceability requirements for food and beverage businesses in their respective regions:
The European Union’s General Food Law of 2002 includes Regulation (EC) No. 178/2002, which requires that companies have a comprehensive traceability system to protect consumers from the risk of contaminations in the supply chain.
The UK—still an EU member at the time of the General Food Law’s passing—still bases its own traceability requirements on those same principles post-Brexit, though it is now the responsibility of the Food Standards Agency (FSA) to enforce compliance.
Meanwhile in the U.S., the Food Safety Modernization Act (FSMA) of 2011 brought with it comparable traceability standards in Section 204, which is now known as the Food Traceability Final Rule and slated for enforcement starting July 2028. The new requirements laid out in this regulation include recording all Key Data Elements (KDEs) at all Critical Tracking Points (CTPs) for the 16 categories of food listed on the Food Traceability List (FTL). Businesses handling FTL foods must also have a detailed traceability plan and use traceability lot codes (TLCs) in an established format.
The consequences of non-compliance with the Food Traceability Final Rule and other countries’ traceability legislation typically range from penalties and fines to temporary or even permanent closure. That underscores the need for food and beverage businesses like yours to have a digital solution—like an industry-specific food ERP—to assist in the collection and management of traceability data, as well as a culture that encourages accountability, due diligence and thorough training.
2. Ensuring Food Safety and Recall Readiness
Traceability and food safety will always be inextricably linked, due in no small part to the fact that complete bidirectional tracking of ingredients and products is necessary to determine the source of contaminations and isolate affected items. The stats show that the industry has plenty of room for improvement on this front, with the World Health Organization indicating that more than 7% of the planet’s roughly 8 billion people[JM1] succumb to foodborne illnesses annually.
The effects are far worse than an upset stomach, too—420,000 die from these incidents each year, equating to a loss of 33 million healthy life years (DALYs). That makes it clear that structuring your traceability processes and systems in a way that allows you to best safeguard consumers from negative outcomes is an imperative, not only for the sake of public health but also to protect your brand reputation.
Undeclared allergens are responsible for more than half of all food safety emergencies[JM2] , so you should educate your teams on the ingredients that are most problematic, take special care when using them and ensure they are segregated from other materials during shipment and storage. The U.S. Food and Drug Administration (FDA) has published a list of nine foods with the highest risk, while the FSA has a list of 14, the same as the European Food Standards Authority (EFSA).
You also need to put a thorough and effective recall plan in place to be completely prepared in the case of the unthinkable. First, you’ll need to gather a trained and trusted group from your internal teams to spearhead your efforts, and then you can use these steps as a starting point for your complete approach:
Alert and activate your recall team.
Determine the severity of the threat and its origin either outside or within your facilities.
Issue all necessary communications, including those to enforcement agencies.
Put a hold on outbound shipments and isolate all affected products.
Set a course of action for the withdrawal and destruction of contaminated goods.
File all required paperwork to maintain total compliance with regulations.
A purpose-built ERP can help prevent food safety emergencies from occurring in the first place by giving you visibility into the path your materials take from source to factory floor and onward. That allows you to keep track of shared surfaces and streamline allergen management across the supply chain.
Furthermore, an advanced system like Aptean Food & Beverage ERP can streamline the recall process by automating certain steps and making the determination of a contamination’s origin much simpler with complete traceability information. Time is of the essence when issues like this do occur, so it pays to have the best possible solution in place to improve your performance in the crunch.
3. Providing Full Product Transparency
Another reason that food traceability is so vital is the increasing demand on the part of consumers for clear ingredient, product and sourcing information. According to ForFarming, 93% of consumers say it’s important for brands and manufacturers to provide detailed information about what is in food and how it’s made.
Thankfully, sound food traceability procedures help you provide shoppers with the transparency they desire. When you know at a glance where your materials came from and how they were made—and that your trading partners are certified, compliant with all laws and following sustainable practices—you can confidently present the facts on product packaging so that consumers can be fully informed.
What’s more, with an ERP platform in place, you can automate your data collection process by integrating the software with handheld barcode and QR code scanners, ensuring accuracy and updating your database in real time. It can then be easily carried over to product artwork and labels to ensure visibility and make all necessary declarations for allergens or other health considerations.
Today’s consumers have high expectations for the brands they support, and they have plenty of options to choose from. Being fully transparent with ingredient and product details, so that consumers can be assured that what they’re eating is healthy and was produced ethically, is best enabled by a specialist food ERP.
4. Avoiding Food Fraud
Food fraud—the intentional misrepresentation of food products, typically for economic gain—is a growing concern. FoodNavigator reports that instances have risen tenfold in the past four years and now cost the global economy approximately $40 billion USD annually. It has serious impacts on consumer trust and food safety, representing serious risk that your business must guard against.
The most common forms of this crime are substitution (often swapping a more valuable ingredient for a cheaper one), mislabeling (especially with false origin information) and counterfeiting. Dilution or use of fillers is also considered food fraud, as are concealment of spoilage or damage and addition of substances not approved for use in consumables.
With the traceability features of an industry-specific food ERP solution, your company will have the tools it needs to prevent food fraud, including full visibility into supplier details, certificates, batch numbers and more. ERPs also offer the capability to pre-select approved vendors and allow users to order only from those sources, as well as recipe control that prevents unauthorized alterations.
Beverages, dairy products and seafood are among the most frequently affected product categories when it comes to food fraud, but fraudulent nuts, seeds and eggs are becoming more common. Regardless of what items your organization deals with, you need a reliable defense against this crime, as it can result in bad publicity and public health emergencies.
Aptean Food & Beverage ERP: The Superior Solution for Complete Traceability
In this post, we’ve focused on the traceability features of food ERPs, but if you haven’t implemented a system of any kind yet, you’ll need to evaluate the options in the marketplace and determine what the best traceability software for your company really is. There are plenty of alternatives on offer, and it will be up to you to find the best fit for your organization.
To demonstrate the appeal of ERP solutions, though, we should stress that there’s much more to love about these all-in-one platforms. In truth, they’re organization-wide interfaces for collaboration, with functions and tools dedicated to different departments and areas of operations, all developed to give businesses like yours a competitive edge.
That’s especially true of our industry-specific food and beverage solution, Aptean Food & Beverage ERP, which has been built upon the strength of decades of collective industry experience and in-depth understanding of best practices for food and beverage companies. We’ve also created a full suite of modules to suit the unique challenges that highly specialized operations need, like catch weight management for meat and seafood providers and consignment tracking for fresh produce growers.
Additionally, we're an industry-recognized provider offering solutions on the SaaS model with cloud hosting, giving you the flexibility to select a lightweight deployment method with lower up-front costs, greater security and 99.9% uptime. Plus, our system leverages robust, unique and industry-specific technology built on an underlying Microsoft Dynamics 365 Business Central platform, lending it familiarity and a user-friendly interface.
Finally, you should know that with Aptean, you’ll always have access to the latest technological innovations. We’re proud to put artificial intelligence (AI) at the core of everything we do, and we’re excited to bring more and more of our solutions to the all-in-one AppCentral platform, our own suite of AI tools and pre-connected applications to streamline your end-to-end process.
So, ready to hear more about Aptean Food & Beverage ERP and how it can improve your company’s approach to traceability in food manufacturing? Reach out to us today, or request a personalized demo.
Empieza a aumentar la trazabilidad en tu operación
Si estás listo para llevar tu negocio de alimentos o bebidas al siguiente nivel, nos encantaría ayudarte.
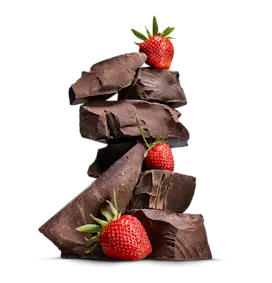