Get in touch today to speak to an expert in your industry
Discover the benefits of software purpose-designed for your industry—from faster implementation to greater efficiency across your entire business.
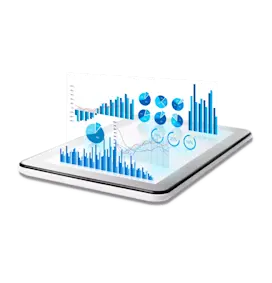
Discover the benefits of software purpose-designed for your industry—from faster implementation to greater efficiency across your entire business.