How ERP Data Management Keeps Critical Information Straight
How ERP Data Management Keeps Critical Information Straight
How ERP Data Management Keeps Critical Information Straight
12 Dec 2019
Andy Pickard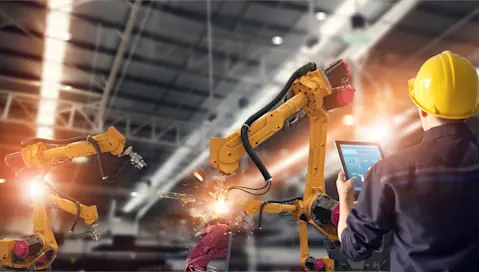
In today’s data-rich world, numbers drive almost every element of business decisions. As the technology that allows us to gather data simultaneously becomes more affordable and more capable of gathering deeper information, companies are going all-in on Industry 4.0. The same holds true for manufacturers. According to research from IndustryWeek and Kronos, “enhanced data availability” is predicted to be manufacturers’ top priority among high-growth technologies in the coming decade.
Yes, it’s valuable to collect the data from machines across the shop floor. But more than that, it’s important we continue to find innovative ways to utilize the data that’s been gathered. After all, what good are hours of data gathered from a critical piece of machinery if it’s not used to determine how much output can be expected?
The Disconnect Between Data Gathering and Data Utilization
As demand grows for faster output and more complex offerings, manufacturers can’t afford any downtime. Disjointed schedules can lead to productivity loss and stagnancies of flow in operations. Gathering and utilizing data can help manufacturers avoid these productivity losses; by measuring and analyzing actual run times, you can more effectively predict future efficiencies and schedules.
There are two components to this process of determining “normal” operations: data gathering and data utilization. You can gather machinery data using sensors, but how are you storing that data, and how are you putting it to use? Many manufacturers are still stuck using manual processes – they keep all data in an Excel spreadsheet or on a whiteboard or even on Post-It notes. Because most manufacturers collect data from numerous sources and store it on different devices, data management through spreadsheets or on paper can lead to duplicative, misinformed processes.
Think about the tasks beyond real-time operations – e.g. communication exchanges or employee schedules. While these tasks may not seem immediately connected to whether a machine is offline, look deeper. Understanding what conversations have already taken place around fixing the machine, or whether employees will need to be reassigned because of downtime, are important elements in keeping the factory up to date. However, these types of data may not be tracked in the same spreadsheet, and often times they might be trapped in an email. Management loses the context they need to keep things running smoothly.
Bottom line: poor data storage habits cause a disconnect between data gathering and data utilization. If your data is out-of-date or saved in an inaccessible folder, you lose a critical decision-making component. In an industry where every second counts, that could be a costly error.
A Single Source Across Systems
In response to the increased emphasis on data gathering and utilization in the factory and the problems associated with manual data storage, enterprise resource planning (ERP) solutions have become a more prominent answer for data management.
An ERP can provide manufacturers with a single solution for collecting data and producing automated reports. This gives users better control over their operations system-wide. You can cut down on the number of spreadsheets on your desktop or binders cluttering your office by storing all of your data on one computerized system. You can integrate core processes and facilitate a consistent stream of data between systems in real-time. Because an ERP solution puts all of your data in one location, and there’s no longer the administrative burden of manual data entry, workers can finally focus on the responsibilities they were hired to complete.
So what’s next? If you’re ready to move away from manual data management toward an ERP, you’ll have plenty of options – but not all are right for every factory. Start by considering your operations: discrete manufacturers face a unique set of challenges – your product components must be assembled in a precise order to ensure quality.
Aptean’s Made2Manage ERP is designed specifically for discrete manufacturers. Made2Manage delivers sophisticated planning and scheduling tools that empower users to create more accurate plans and monitor execution. Using the ERP, management can understand how all the pieces of the operational puzzle fit together because the data feeds into one place—like how many employees need to be scheduled based on production timetables or how repairs are coming along on a malfunctioning forklift. This kind of information helps streamline operations and improves visibility throughout the entire supply chain.
Move Away From Manual
If pen-and-paper or spreadsheets are your main form of data storage, your best strategy is to adopt technology that ensures every piece of data is accurate, up-to-date and accessible. Choosing an ERP to connect disparate systems and empower optimal data utilization will help you achieve your goals, and ensure you can remain competitive in an industry where “do more with less” has become the mantra.
Want to learn more about how Made2Manage can unify your data? Reach out here.
Request a callback from a manufacturing ERP expert
We’ve got the specialised ERP solutions you need to conquer your industry challenges.
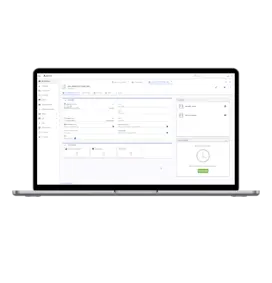