What It Takes To Be Fully Recall-Ready in the Food and Beverage Industry
What It Takes To Be Fully Recall-Ready in the Food and Beverage Industry
What It Takes To Be Fully Recall-Ready in the Food and Beverage Industry
Aug 3, 2022
John McCurdy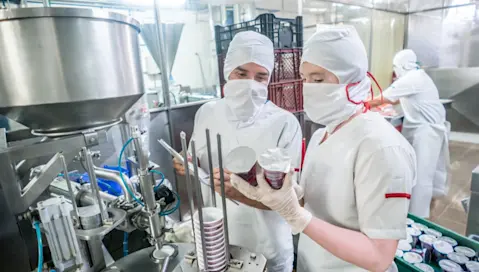
If the mere phrase “product recall” sends a cold chill down your spine, you’re not alone. Food and beverage industry professionals the world over share your trepidation and definitely want to avoid the average $10 million cost these urgent incidents bring with them.
There’s a real human cost to food safety emergencies, too, as the World Health Organization reports that more than 600 million cases of foodborne diseases are recorded each year, and 420,000 of those result in death. Needless to say, that makes prioritizing the protection of end consumers from such unfortunate outcomes and maintaining your brand reputation as a name to trust an absolute imperative.
Really, though, there’s no reason to fear or feel threatened—assuming your operations are fully recall-ready, that is. But what exactly does it take to prepare for these events, and how can a purpose-built enterprise resource planning (ERP) solution help you enhance your strategy and maintain better food safety overall?
We’re here to fill you in, so let’s begin with the basics.
Know What’s Required
It may surprise you to learn that most recalls are voluntary. That makes sense, though, when you consider that being accountable, open and honest when it comes to consumer health and safety is crucial for brand reputation—and owning up to mistakes and doing all you can to eliminate risks will spare you the worst fines and penalties from enforcement agencies.
When it comes to what’s required of a food and beverage business that has decided to issue a recall, the process varies from region to region depending on the relevant government authority:
In the U.S., the Food and Drug Administration (FDA) has fairly extensive guidance on the procedure to follow for a recall, including identification of its depth and issuance of both an official letter to notify the public and periodic status reports. Of note, the Food Safety Modernization Act of 2011 (FSMA) does give the FDA authority to make a recall mandatory if the company responsible for a food safety emergency does not take action on its own.
In the UK, the Food Standards Agency (FSA) provides comprehensive instructions for recalls, from the information gathering stage to the destruction and disposal of affected goods.
In the EU, the General Food Law Regulation provides for four measures—the establishment of the Rapid Alert System for Food and Feed (RASFF), the creation of the Standing Committee on Plants, Animals, Food and Feed (PAFF Committee), adoption of emergency measures and, most importantly, general plan for crisis management.
As the saying goes, “knowledge is power.” Having a firm grasp on what a recall entails and what will be expected of your business should you find yourself in an unfortunate situation will go a long way in preparing you for a potential recall.
Create a Recall Plan
The next step in getting fully recall-ready will be to form an internal plan for quickly and effectively launching into action and completing the process in an efficient, but thorough, fashion. These basic steps can form the foundation on which you build out your more complete and personalized plan:
Prior to any incidents occurring, create a dedicated internal recall team that includes employees across multiple functions.
Once a contamination or other product safety concern has been identified, activate your team and record what pertinent information is readily available.
Evaluate the level of risk and assess the scope and severity of the issue.
Issue all necessary communications, especially those to the relevant government agency for your location.
Place an immediate hold on affected products and trace the contamination to its source.
Initiate the recall and properly dispose of all withdrawn items.
Carefully complete and file all necessary documents to ensure full compliance.
While none of the aforementioned government agencies prescribe a concrete timeframe for a recall, you no doubt will want to execute on your plan as soon as possible—just make sure not to cut corners in the process. Also, how long it takes will vary depending on how quickly the source can be identified, how many products must be withdrawn and how far “downstream” the affected goods have traveled, but in the case of the most severe incidents—deemed “Class 1” in the U.S.—time is of the essence.
Prioritize Good Training
A well-trained and diligent team of professionals is one of the best possible safeguards against food safety emergencies and recalls. They need to be well-educated on proper procedures, including sanitation processes, allergen management, use of safety gear like gloves and masks, documentation of incidents and your business’s specialized internal processes.
Keep in mind too that as circumstances change—novel products are introduced to your lineup, equipment is replaced or new systems are implemented—additional training should be provided. Everyone must be up to speed in order to minimize the chances that you’ll need to issue a recall, and good instruction should never be foregone for the sake of convenience.
It’s also a smart move to practice your recall plan and conduct regular internal food safety audits so that your staff are aware of what it’s like to jump into action and investigate an issue. Gaining an understanding of the challenges involved and how it feels to act with confidence and agility in the moment will serve them well should a real emergency occur.
Take Advantage of Technology
Putting in place an ERP solution designed specifically for food and beverage companies is another critically important step in optimizing your approach to food safety and maximizing recall readiness. That’s because these cross-functional platforms for all areas of operations are packed with features that will have you fully equipped for the tasks at hand.
For example, there are the dedicated traceability tools that modern systems offer, which make maintaining complete bi-directional tracking of raw materials and finished goods a much simpler matter. By logging all ingredient and product data at each point in the supply chain—both outside and inside your facilities—you’ll have visibility and immediate access to a digital record of the path each lot or individual item takes.
ERPs can also be used to deploy regular alerts that ensure all necessary safety and sanitation checks occur each and every time, which is a prudent move considering how busy food factories can be during normal day-to-day activities, let alone high-volume production runs. Many also provide allergen management functionalities, including the identification of higher-risk ingredients in your recipes.
Truly advanced solutions—like our own Aptean Food & Beverage ERP—can even automate portions of the recall process, including expedited tracking to the source of any contaminations and issuance of necessary communications to affected parties. That lets your highly qualified personnel concentrate on other critical steps like organizing withdrawal efforts and properly documenting the incident.
Trust Aptean for the Software to Improve Your Recall Readiness
We’ve outlined some of the most important information and best practices for food and beverage product recalls, as well as how ERP solutions give your operations several significant advantages should your business face one of these unfortunate incidents. Hopefully, that’s got you ready and eager to put this advice into practice, but we recognize you may still have some questions, especially if ERP technology is new to you.
If you search online to find the ERP options available on the market, you’ll be inundated with choices, with most—if not all—claiming to be able to solve your problems and ensure good results. Of course, you know that’s too good to be true, but it can still be difficult to determine what sets apart a superior system from the rest.
The most important hallmark of a good ERP system is that it was built specifically for food and beverage businesses using real-world experience and in-depth expertise with the industry. Here at Aptean, we’re proud to have decades of collective knowledge, and our team has a track record of deploying our cutting-edge offering for companies like yours around the world.
We also offer flexible cloud implementations that help you stay nimble and ready to react quickly should any food safety emergencies arise within your organization. They’re backed by dedicated cloud IT teams that offer outstanding support, as well as redundant offsite servers for 99.9% uptime and superior cybersecurity.
So, ready to hear more about Aptean Food & Beverage ERP and how it can help your food and beverage business become truly recall-ready? Contact us today, or schedule a personalized demo.
How To Thrive During Food and Beverage Market Turbulence
Prioritizing modernization, optimization and a sound strategy is necessary for success in the food and beverage industry. Increase operational agility in a continually changing (and often unpredictable) manufacturing landscape.
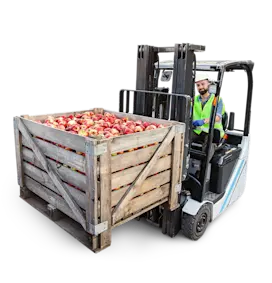