Featured in this post
How Software Helps You Unlock Manufacturing Process Improvement at Every Stage
How Software Helps You Unlock Manufacturing Process Improvement at Every Stage
Sep 2, 2024
Aptean Staff Writer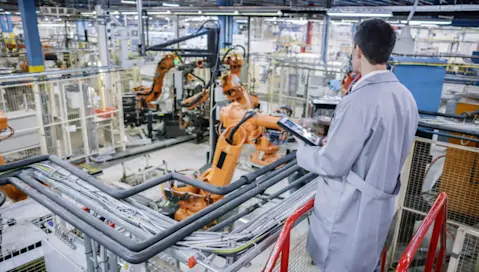
External pressures are a constant for your manufacturing business. Whether it’s changing customer demands, supply chain disruptions, rising operational costs or tough competition, a range of factors make it hard for you to stay successful.
That means your business must evolve as the industry does—you can't just do things the same old way. Every part of your operation, from designing products to getting them to customers, needs to be optimized for today’s conditions.
But where do you begin with manufacturing process improvement? It's easy to feel overwhelmed when you think about all the moving parts in your operation. How do you identify the areas that need the most attention? And once you do, how do you make changes without causing disruptions? These are all typical concerns, but thankfully there's a way to tackle them effectively.
Technology is your ally in this journey. It enables you to identify problem areas and guides you through making meaningful changes. With the right software, you can monitor, analyze and optimize your operations in real time. There’s manufacturing software available to power every stage of your operations—from product lifecycle management (PLM) for optimizing development to truck routing and scheduling software to reliably get your products to your customers on time. These systems are more than just digital tools; they're strategic assets that help you automate workflows, reduce waste, increase efficiency and boost productivity.
In this blog, you'll discover how software can bolster process optimization in manufacturing—helping you tackle your daily challenges and transform your operation into a lean, efficient and highly productive machine.
Where To Start With Manufacturing Process Improvement
Let’s address those common questions we hear when businesses are facing the challenge of optimizing their manufacturing operations. Firstly: Where do you begin with manufacturing process improvement?
The answer is the same for all manufacturers—digital transformation planning. It’s the first step toward revolutionizing how your manufacturing operation works.
Digital transformation is not just about adding new tools—it's about reshaping how your entire operation works. By planning a thorough digital transformation journey, you can enhance every part of your business, improving efficiency, making smarter decisions and delivering better customer value.
Manufacturing process optimization is a continuous journey that requires strategic thinking and the right tools. That’s why planning a clear, cohesive digital transformation roadmap that combines software and processes is critical, instead of an “as and when” approach to system implementation. It allows you to achieve broader business objectives and capture optimal return on investment (ROI), unlocking a cost-effective, high-quality production process that keeps you competitive and drives ongoing success.
Understanding Manufacturing Process Improvement Approaches
Now you’re trying to plan out your digital transformation priorities, the next question is logically: How do you identify the areas that need the most attention?
It starts with understanding and implementing the key methodologies that guide process improvement. The following approaches help you spot inefficiencies and make intelligent changes, providing a roadmap for continuous improvement and ensuring you’re always moving towards better performance. They also work hand in hand with manufacturing optimization software to streamline processes and boost efficiency.
Lean Manufacturing
Lean manufacturing is a beacon of efficiency and resourcefulness, focusing on reducing waste and maximizing productivity. This method emphasizes creating value for the customer while ensuring the efficient use of resources. By identifying and cutting out activities that don't add value, Lean methodology helps streamline operations, reduce costs and boost productivity.
One key concept in Lean is the Six Big Losses, which details the types of waste that can occur in your manufacturing process:
The Six Big Losses are:
Mechanical Downtime, Loss Category: Utilization (Availability)
Set-up and Changeovers, Loss Category: Utilization (Availability)
Idling and Minor Stoppages, Loss Category: Rate Loss (Performance)
Reduced Speed Operation, Loss Category: Rate Loss (Performance)
Scrap and Rework, Loss Category: Yield (Quality)
Startup Losses, Loss Category: Yield (Quality)
By categorizing the Six Big Losses into “availability”, “performance” and “yield”, you can systematically investigate and address issues in your manufacturing processes. This approach provides a clear framework for problem-solving, giving you confidence in your ability to improve your business’s performance.
Six Sigma
Six Sigma is a method that values precision and control, aiming to reduce variation and improve quality through statistical methods. It follows a structured approach known as DMAIC: define, measure, analyze, improve and control. This method helps you identify problems, analyze their causes and implement precise improvements. By controlling and reducing variability in your processes, Six Sigma ensures that you consistently meet quality standards and deliver products that satisfy your customers.
Plan-Do-Check-Act (PDCA)
PDCA is an iterative continuous improvement model. As the name suggests, it involves planning changes, implementing them, checking their effectiveness and acting on the results. PDCA keeps you in a constant loop of improvement, allowing you to refine processes over time. This approach ensures that your manufacturing operations are always evolving and improving.
Leveraging Software for End-To-End Manufacturing Process Improvement
So now you have a thorough plan, and a solid idea of which areas need your attention, it’s time to consider: How do you make the necessary changes and enhancements without causing disruptions?
To do this and improve your manufacturing process, you’ll not only need to implement some of the methodologies we’ve discussed, but deploy specialized software solutions that enhance each facet of your operation, too. Here's how various manufacturing software systems contribute to optimizing your processes step by step:
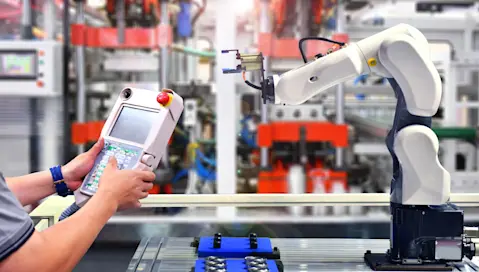
New Product Design and Development With PLM Software
Before your product can ever hit the shop floor, it must pass through a thorough design and development process. In this stage it’s crucial to balance innovation, financial viability and compliance to satisfy customer, regulatory and business requirements.
PLM software helps your teams do just that and is essential for managing the entire lifecycle of a product, from concept to disposal. As a fully digital platform, it centralizes data and processes, ensuring efficient new product development (NPD). With tools for each of your development teams, a PLM system facilitates timely completion of tasks and easy access to critical information, optimizing this first critical step of your manufacturing process.
With the right PLM software, you’re able to streamline design and development processes, reduce associated costs, boost product quality and ultimately, introduce your new products to the market at a faster pace. When being the first can make all the difference, this speed is a game-changer, and reliably delivering quality, on-target products is sure to promote customer loyalty.
Production Planning With ERP
Once your product design is set, the focus shifts to production. As you know, managing the flow of orders, resources, inventory and schedules is complex; this is where manufacturing-specific enterprise resource planning (ERP) software comes in. This critical cross-functional system gives you an accurate, real-time view of your needs and helps you predict demand accurately. This means better production planning and scheduling, avoiding costly stockouts or overstocks, and boosting customer satisfaction with on-time fulfillment/availability.
With accurate data on capacity, current stock and resource availability an ERP helps you automate and streamline production processes, too. So, you’ll have better visibility, lower costs and more control over this fundamental step in your manufacturing process. For example, you can organize your production floor by work order or batch ticket, boosting productivity, maximizing resource utilization and helping you deliver on-time, in-full. It's a win-win: you get more done while keeping customers happy.
Additionally, an ERP system provides comprehensive visibility and enables proactive responses when things go wrong. For example, what if ingredients or raw materials are delayed? Armed with real-time visibility and flexible production planning tools, you can make more informed decisions, like prioritizing tasks that don't need the missing items.
By leveraging ERP, you can swiftly respond to changes in demand or supply chain disruptions—ensuring that your production operations are efficient, cost-effective and in sync with your overall business strategy.
Shop Floor Productivity With OEE
Once production is underway, maintaining efficiency on the shop floor is critical. Implementing overall equipment effectiveness (OEE) software makes a significant difference here, leading to reliable plan attainment, improved productivity and reduced waste.
We’re sure you know that OEE—actual productive time vs. planned production time—is a crucial metric for manufacturers seeking to elevate productivity and identify areas for improvement. OEE software automatically collects and analyzes data to calculate your OEE score, offering real-time visibility into shop floor performance. This makes it easier for you to make strategic data-driven decisions on where to invest in improvements, whether it's training, maintenance or new equipment.
Advanced features like cost monitoring, mobile accessibility and direct integration with machinery also give you the tools to monitor and improve production efficiency on the fly. This real-time insight is crucial for making timely adjustments that keep your operations running smoothly every day. If you often miss production targets, struggle with low ROI or deal with frequent rework, it might be time to consider OEE software. It helps address these issues by minimizing short stops, idling time and yield losses—promoting accountability, reducing scrap and boosting customer satisfaction with on-time order fulfillment.
Equipment Availability With EAM
Now that your designers have created an attractive product, you’ve managed the inventory required to make it and efficiently scheduled its production, the last thing you need is disorganized maintenance schedules or unexpected equipment downtime to disrupt your workflow. That’s where enterprise asset management (EAM) software truly shines.
EAM software optimizes the utilization of your physical assets, such as machinery and equipment—managing their entire lifecycle, from acquisition to disposal to ensure you get the most out of your investment. Firstly, EAM provides a full digital record of each of your assets, with remote monitoring providing current data and alerts when anomalies occur, while historical records provide complete visibility into previous maintenance, work orders and failure codes.
Combining all of this data with advanced preventative maintenance features, EAM software can predict when a machine is likely to fail and recommend maintenance before that happens. This means you can better schedule maintenance to keep production on track and even enable automation of key tasks such as parts ordering.
All in all, with an EAM system, you can ensure that your equipment is always available and ready to perform, keeping your production line running smoothly and maximizing profitability.
Delivery With TMS Tools
Now, we’re on the home stretch. Your product has been successfully manufactured and the next step is getting it to your customers, when and where they want it. One poor delivery can set off a chain reaction, ultimately impacting customer loyalty and future profitability. Conversely, an efficient, on-time delivery helps protect your profit margins in the final mile while maintaining customer satisfaction. Thankfully, there are a range of transportation management tools to help.
Firstly, a full TMS can take orders from your ERP system and present your best transit options—whether you’re using a range of third-parties or a mixture of carriers and your own fleet of vehicles. Not only does this help you centralize transportation planning while maintaining efficient local execution, it also ensures you can maximize efficiency, reducing costs while ensuring your product gets to where it needs to be on time.
Next, route optimization software empowers you to plan the most efficient delivery routes taking into account all of your business-specific variables, including customer time windows and driver availability. This significantly reduces your transportation costs and saves time. By optimizing routes in this way, you also ensure that your products reach customers faster and with fewer delays, giving you greater control over your delivery operations and customer delivery experience. Plus, advanced systems offer strategic route planning tools so you can enact continuous process improvements.
Speaking of customer service, electronic proof of delivery (ePOD) systems are designed to create outstanding experiences in the final mile while helping you save money. Your drivers follow consistent, pre-defined processes that ensure smoother and quicker on-site interactions while automated customer communications keep your clients informed throughout the delivery process. ePOD software also boosts efficiency by providing real-time visibility into delivery operations, simplifying driver tasks and ensuring that more deliveries can be completed within the same time frame.
Creating a Continuous Improvement Loop With BI
As you know, making informed decisions is necessary to run your business smoothly. While each of the solutions we’ve discussed here can help you bolster manufacturing process optimization straight out of the gate, to be truly future-ready, you need an additional layer of actionable insights.
Enter business intelligence (BI)—efficiently gathering and analyzing data from various sources across your organization, including your ERP system, to help you create a continuous improvement loop. BI software provides clear visualizations and analytical tools to guide your strategic choices. If you’re struggling with data overload, inaccurate reports or slow decision-making, BI could be the solution you've been searching for.
BI tools are designed to handle complex data from spreadsheets, databases and other systems and consolidate this information into clear, actionable insights. The best part? You can customize reports to fit each of your departmental needs, making data analysis more relevant and ensuring your specific business needs are met. With this data at your fingertips, you can easily implement additional manufacturing process optimizations.
BI software also allows you to track key performance indicators (KPIs) over time, which lets you see if your changes are delivering the desired results. If they're not, you can adjust your strategies and continue refining your processes. This ongoing analysis, improvement and adjustment cycle ensures that your manufacturing operation is always moving forward.
Accelerate Your Manufacturing Process Optimization With Aptean's Software Suite
You can transform your manufacturing process into a well-oiled machine by integrating the right software solutions at each stage. Whether it’s PLM for enhancing NPD, ERP for efficient resource planning or OEE for boosting shop floor productivity, digital technologies can accelerate process optimization in manufacturing operations helping you drive efficiency, profitability and growth.
Unfortunately, implementing basic systems or those not tailored to suit your specific manufacturing industry can lead to costly customizations, failure to realize the intended benefits and a reduced ROI.
At Aptean, we’ve spent decades delivering proven industry-specific software solutions to businesses like yours. Our systems offer specialized features for a range of both process and discrete manufacturing verticals, including food and beverages, cosmetics and apparel. And, with cloud deployments, thorough development pipelines and a focus on incorporating innovations like AI, our software remains at the cutting edge, ensuring that you’re always Ready for What’s Next, Now®.
What’s more, we know that implementing these tools is just the beginning. Our in-house teams can provide lifetime support and consultation, helping you analyze performance, adjust strategies and adapt to market changes.
Equip your business with the right technology and start seeing significant, tangible improvements in your manufacturing process today with Aptean.
Ready to take the next step? Explore our suite of manufacturing software solutions designed to help you achieve your goals and secure your competitive edge. Contact us now to learn how we can support your journey toward manufacturing process improvement.
Get in touch today to speak to a software industry expert
To grow your business, you need a purpose-built ERP for process manufacturing. We're ready to help—reach out today for your free no-obligation consultation.
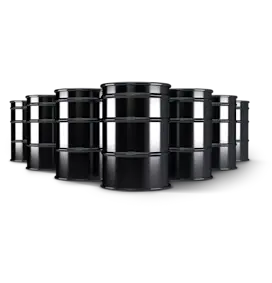